The History of Nylon
The creation of nylon in 1935 brought with it the advancement of many traditional products. From toothbrushes and stockings to tires and rope, nylon has long been referred to as the “miracle fiber” because of its amazing multi-purpose fibrous form. However, there’s more to nylon than the synthetically manufactured fibers produced in a lab. This plastic can be morphed into a variety of other shapes, including general-purpose cast and extruded nylon.
Recognizing nylon solely for its fibrous versatility would be doing it a disservice. Instead, nylon should be referred to as the “miracle plastic” because of its capabilities in almost every industry. In this article, we will focus on why cast and extruded nylon should be considered for your projects and how analyzing the differences between the two could help improve your production.

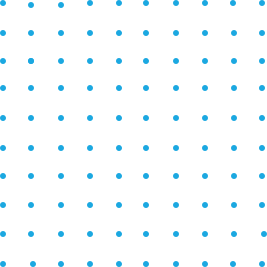
An Expert is just around the corner.
With over 100 years of combined product knowledge and industry experience, we are confident our plastics experts can help you find a solution for your application.
Understanding Cast and Extruded Nylon
Nylon is one of the most popular engineered thermoplastics in the world. This versatile material is used in many industries and countless applications. Two common types of nylon plastic material are cast nylon and extruded nylon. While these materials share many similarities, they also have important differences. Understanding these differences will help you choose the right nylon product for your needs.
Why Choose Nylon Plastic Material?
Nylon is widely used because of its excellent benefits and mechanical properties. It is tough, strong, and has a low coefficient of friction, which means it reduces wear and tear when used in moving parts. Nylon plastic material is also a cost-effective solution. Compared to materials like metal or rubber, nylon parts are less expensive, making them ideal for budget-friendly projects.
Advantages of Cast Nylon
Although cast and extruded nylon are very similar, cast nylon does hold a few advantages over its extruded counterpart:
Cost Efficiency: Cast nylon is usually cheaper to produce, especially for larger or more complex parts. This makes it a great option for large-scale projects.
Lower Stress Levels: Cast nylon materials naturally have lower internal stress compared to extruded nylon. This means they are easier to machine or fabricate, have better dimensional stability, and offer higher tensile and compressive strength.
Heat Resistance: Both cast and extruded nylon can handle high temperatures, but cast nylon has a slightly higher operating temperature. If your project involves heat-sensitive parts, cast nylon may be the better choice.
These qualities make cast nylon ideal for applications that require durability, precision, and reliability.
What Are Nylon Plastic Sheet, Rod, and Tube Used For?
At Piedmont Plastics, we offer a variety of nylon products, including cast nylon and extruded nylon. Cast nylon comes in customizable sizes and colors, while extruded nylon is typically available in nylon 6/6 rod and nylon sheet options in a natural light tan color.
Both cast and extruded nylon are used in similar industries, but the choice of material depends on the specific application.
Common Nylon Applications
Ordering Wholesale Nylon Materials
If you are looking to buy nylon products for your project, Piedmont Plastics is your trusted wholesale distributor of nylon materials. Whether you need wholesale cast nylon or extruded nylon products, we can help you find the right materials. Our team of experts is ready to answer your questions and assist with your order.
Ready to Purchase?
To learn more about nylon plastic material and how it can improve your machines or products, visit our website or contact us today to place an order for nylon products!
Get a Quote for Nylon Materials