Best Plastics for Power Industry Use
In power generation, insulation is vital in electrical and electronic equipment such as transformers, circuit breakers, and cables to ensure electricity's safe and efficient transmission. Proper insulation prevents electrical currents from leaking or short-circuiting, which protects equipment, maintains system stability, and prevents hazards such as electrical shocks and fires. In high-voltage environments like power plants and substations, the right insulating materials help maintain the integrity of these critical components.
Selecting the right plastic material for insulation is essential for ensuring safety, durability, and performance in these demanding conditions. Insulating plastics must offer high dielectric strength, thermal resistance, and mechanical durability to withstand harsh environments, including extreme temperatures, UV exposure, chemicals, and moisture.
Choosing the optimal insulating plastic increases the reliability of power generation systems, reduces maintenance costs, and ensures compliance with safety standards, making it a primary part of power generation infrastructure.

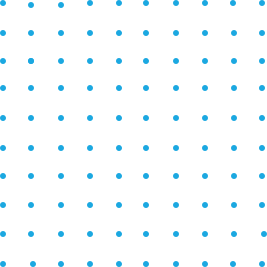
An Expert is just around the corner.
With over 100 years of combined product knowledge and industry experience, we are confident our plastics experts can help you find a solution for your application.
Key Properties of Effective Insulated Plastics
High dielectric strength and low conductivity are critical for insulating materials used in power generation. These materials prevent electrical currents from passing through unintended paths, reducing the risk of short circuits and electrical failures. These materials must also resist heat, UV radiation, chemicals, and moisture to maintain their performance and structural integrity in harsh environments. Mechanical strength and impact resistance are critical for guaranteeing durability under mechanical stress, while flame retardance adds an extra layer of safety by minimizing fire hazards.
Additionally, thermoformability allows for easy shaping and customization to fit specific applications, and hydrolytic stability ensures that the material retains its properties and does not degrade when exposed to water or moisture over extended periods.
Top Insulated Plastics for Electrical Applications
When choosing insulating plastics for electronic applications, it is critical to understand each type of plastic's unique characteristics. Different plastics provide varying levels of dielectric strength, impact resistance, heat resistance, and other notable properties that can considerably affect their suitability for specific uses.
Below is an overview of some popular insulating plastics:
Best Insulating Plastics
-
Specialty Acrylic Sheet
Acrylic is a highly versatile plastic that is easily fabricated and offers superior clarity and durability in a range of applications. This makes it an ideal choice for products requiring precision, resilience, and a high-end appearance.
-
ABS
Acrylonitrile butadiene styrene is a durable, impact-resistant material commonly used in automotive components, consumer goods, and protective housings.
-
Extruded Nylon
Piedmont Plastics carries FDA-compliant extruded nylon 6/6 rod and sheet in a natural light tan color for self-lubricating or slide-type applications.
-
Polycarbonate
Polycarbonate is a high-performance, impact-resistant thermoplastic known for its clarity, strength, and weatherability, making it suitable for applications such as eyewear lenses, bullet-resistant glass, construction materials, and automotive parts.
These plastics' distinct advantages are:
Acrylic: Excellent optical clarity, insulation, and weather resistance.
Acrylonitrile Butadiene Styrene (ABS): Good dielectric strength, impact resistance, and affordability.
Nylon: High durability, heat resistance, and wear resistance.
Polycarbonate: Superior impact strength, flame retardance, and UV resistance.
Comparing for Different Applications
For high-temperature applications, such as those found in both indoor and outdoor settings where materials must withstand significant heat, Polycarbonate (PC), Polyamide-imide (PAI), and Nylon (Polyamide, PA) are ideal choices due to their exceptional heat resistance, mechanical strength, and flame retardance.
Acrylonitrile Butadiene Styrene (ABS) and Acrylic (PMMA) are better suited for low-temperature environments or those exposed to chemicals. ABS offers good chemical resistance, dielectric strength, and impact resistance at lower costs. At the same time, Acrylic provides excellent optical clarity and weather resistance, making it suitable for outdoor applications where visibility and durability are important.
Specialized Purposes for Insulated Plastics
Insulating plastics are widely used in various electrical applications, such as electrical enclosures, junction boxes, circuit boards, connectors, and arc shields. They provide critical protection against electrical currents, environmental factors, and mechanical impact. In high-performance settings like data centers, automotive electronics, and telecommunications, these materials are chosen for their advanced properties, such as high dielectric strength, thermal stability, and resistance to chemicals and UV radiation.
For example, in data centers, insulating plastics are essential for creating reliable electrical connectors and circuit boards that can withstand continuous operation and high temperatures. Automobile electronics protect sensitive components from heat, vibration, and electrical interference, ensuring vehicle safety and performance.
Additionally, in underground utility installations, insulating plastics are crucial for duct spacers that securely separate and support multiple conduits, protecting them from physical damage, maintaining alignment, and ensuring efficient and organized cable management.
Factors to Consider
When selecting insulated plastics for electrical applications, it's important to consider several key factors to ensure safety, performance, and cost-effectiveness. Here’s a short guide to help you choose the right material:
1. Evaluate Environmental Conditions
Determine the specific environmental factors the plastic must withstand. Choose materials like Polycarbonate (PC), PAI, or Nylon for high-temperature environments. For outdoor use where UV resistance is crucial, consider Polycarbonate or Acrylic. In settings with high humidity or chemical exposure, select ABS or Acrylic for their excellent resistance properties.
2. Check Safety Standards Compliance
Ensure that the selected plastic meets essential safety standards such as NEMA and UL certifications, which are critical for electrical applications. This verification will provide you with the confidence that the material has a suitable fire resistance rating, like UL94 V-0, to provide additional safety in high-risk environments.
3. Consider Cost and Material Availability
Balance the performance needs with budget and availability. For cost-effective and widely available options, consider using ABS for general applications. For specialized or high-demand environments, rest assured that investing in premium materials like PAI, which offers superior heat and electrical insulation properties, is a wise decision.
Need More Information?
Innovations in high-performance polymers are changing the electrical and electronic industries, providing solutions like superior heat resistance, better electrical insulation, and enhanced durability for cutting-edge applications such as 5G, electric vehicles, and renewable energy systems. At the same time, there's a strong push toward more sustainable and recyclable materials that help reduce environmental impact while maintaining top performance.
Consult The Plastics Experts
If you're looking to find the right materials for your projects, Piedmont Plastics, with our extensive experience and expertise, is here to help. Our team can guide you through the options and provide expert advice to ensure you choose the best materials for your specific electrical and electronic needs. Contact us to get started!
Get In Touch