Industrial laminates play a major role in a wide range of modern applications. Comprised of layered substrates—such as paper, cotton, or glass fabric—these laminates are bonded under heat and pressure using thermosetting resins like phenolic, epoxy, melamine, or silicone. The resulting materials combine multiple properties, such as mechanical strength, electrical insulation, and thermal stability, into one engineered solution.
Among these materials, phenolic laminates have gained considerable attention due to their cost-effectiveness, moderate to high strength, and reliable insulating capabilities.

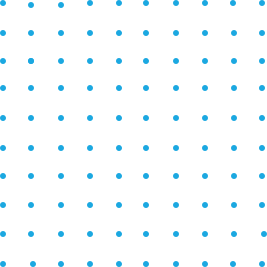
An Expert is just around the corner.
With over 100 years of combined product knowledge and industry experience, we are confident our plastics experts can help you find a solution for your application.
Phenolic Laminate Construction
Phenolic laminates are created by impregnating layers of cellulose-based or fabric-based substrates with phenolic resin. The assembly is then cured under specific temperature and pressure conditions, forming a rigid, dimensionally stable, and highly durable sheet material. This process optimizes the transfer of resin into the substrate so that each layer is fully penetrated. Achieving even resin distribution is essential to ensure uniform electrical, thermal, and mechanical properties. The consistency of resin flow and the uniform compression across the laminate stack defines the ultimate performance and reliability of the finished sheet.
One of the reasons phenolic laminates stand out is their inherent robustness. These resins undergo a condensation reaction at elevated temperatures, creating a crosslinked polymer matrix with strong covalent bonds. This crosslinking process yields a thermoset material that offers a stable dimensional profile and is resistant to a variety of chemicals as well as capable of withstanding moderate to high temperatures.
As a result, phenolic laminates can be engineered for projects requiring protection against mechanical stress, moderate heat, or electrical hazards.
Technical Properties and Advantages
Phenolic laminates stand out in several critical performance areas, particularly where cost-efficient yet reliable insulation is desired. They provide a high dielectric strength suitable for many electromechanical systems, maintain stability under moderate thermal loads, and offer enough mechanical durability for various industrial needs. While certain high-performance laminates—such as glass epoxy materials—may surpass phenolic laminates in extreme conditions, phenolic-based products are still a practical choice in scenarios that balance performance requirements with budget considerations.
🔑 Key Technical Advantages of Phenolic Laminates
-
Electrical Insulation: Phenolic resins combined with paper or cloth substrates deliver robust dielectric strength, effectively preventing leakage or arcing in transformers, generators, and switchgear.
-
Thermal Stability: Although phenolic laminates endure heat commonly generated by motors and relays without compromising insulation or structural integrity, they are not on par with advanced epoxy or polyimide laminates at higher temperatures.
-
Mechanical Durability: Paper-based phenolics excel under moderate mechanical loads, while fabric-reinforced variants (cotton or glass cloth) bolster impact resistance and tensile strength, making them suitable for more demanding applications.
-
Cost-Performance Balance: Phenolic laminates are typically more affordable than high-end laminate options. Their overall material properties often meet the electrical and moderate mechanical demands of industrial settings without unnecessary expense.
Popular Applications
Phenolic laminates play a fundamental role in the electrical and electronics industries, where their high dielectric strength ensures safety and reliability. These laminates are commonly used as insulators for transformers, bus bars, and switch panels, as well as in rotor and stator components for electric motors. Their stability under mid-range temperatures minimizes deformation, making them ideal for precision parts like relay bases and circuit isolators.
In mechanical manufacturing, phenolic laminates provide a cost-effective solution for producing gears, jigs, fixtures, washers, and spacers. Their excellent machinability allows them to be shaped into various configurations without excessive tool wear. At the same time, their shock absorption properties make them suitable for bearing supports that endure vibration or repeated impacts. This combination of durability and affordability makes phenolic laminates a reliable choice for industrial components.
The architectural and structural industries increasingly rely on high-pressure phenolic panels for their strength and versatility. These panels are widely used in rainscreen cladding systems due to their UV resistance, color retention, and fire-resistant formulations, including Class A flame-spread ratings. Their non-porous surfaces resist graffiti and wear, making them particularly valuable for high-traffic urban environments and public buildings, where durability and low maintenance are essential.
Comparison to Other Industrial Laminates
When evaluating phenolic laminates within the broader category of industrial laminates, they are often compared to other materials based on performance, cost, and application-specific requirements.
Two common comparisons are with glass epoxy laminates (e.g., G10 and FR4) and fabric-based phenolics, highlighting the distinct advantages and trade-offs of each.
Comparison with Glass Epoxy Laminates (G10/FR4)
- Glass epoxy laminates excel in high-temperature environments and offer superior dielectric properties and mechanical strength.
- However, they are significantly more expensive and require specialized tooling for fabrication.
- Phenolic laminates are less robust under extreme conditions and more cost-effective and easily machined using standard tools, making them ideal for large-scale or moderate-demand applications.
Comparison Between Fabric-Based and Paper-Based Phenolics
- Fabric-based phenolics use reinforced materials like cotton canvas or glass cloth, providing enhanced mechanical strength and impact resistance.
- These laminates are heavier and more costly, making them suitable for heavy-duty applications with critical mechanical loads.
- Paper-based phenolics focus on electrical insulation and cost efficiency, offering adequate toughness for most industrial and electrical uses without over-engineering for less demanding applications.
Limitations and Considerations
Although phenolic laminates are versatile, potential users should keep certain limitations in mind. One key issue is moisture sensitivity. Prolonged exposure to high humidity may affect the dimensional stability and electrical characteristics of some phenolic laminates, particularly if they are not specifically treated or encapsulated. Using protective coatings or locating phenolic components in controlled environments can alleviate this concern. In scenarios where excessive moisture is unavoidable, materials like glass epoxy laminates may be a better fit due to their lower propensity for water absorption.
Impact resistance is another potential shortcoming when comparing paper-based phenolic laminates to more robust fabric-reinforced laminates or advanced resin systems. Applications with frequent impact, abrasion, or high tensile loads could benefit from phenolics that integrate cotton or glass fabrics or a different laminate family altogether. Cost constraints are also a factor in the decision-making process. While phenolic laminates are generally considered more affordable, certain specialty grades, high-thickness sheets, or products requiring rigorous testing can increase the overall expenditure.
Need Expert Assistance?
As the demand for advanced composites increases, manufacturers innovate with hybrid reinforcements, improved resin chemistries, and sustainable materials. These advancements enhance flame retardancy, reduce moisture absorption, and boost thermal stability while addressing environmental regulations with recycled fibers and eco-friendly resins.
Engineers and designers should evaluate key factors like electrical loads, temperature ranges, mechanical stress, and fire or moisture resistance when selecting a laminate. A thorough cost-benefit analysis, including fabrication ease, product lifespan, and maintenance needs, is essential. Partnering with a trusted supplier ensures access to accurate data sheets and expert recommendations tailored to your requirements.
Consult With The Experts
To explore your options and find the ideal material for your project, contact Piedmont Plastics to speak with a specialist and receive expert guidance!
Send Us A Message