Thermoplastics Explained
Thermoplastics have revolutionized modern industries with their adaptability, durability, and wide range of applications. These versatile polymers offer engineers and designers materials that can be molded and reshaped repeatedly without altering their chemical properties.
Piedmont Plastics supplies various thermoplastic materials for countless applications across the construction, automotive, medical, and consumer goods sectors. Understanding the technical aspects of thermoplastics will help you make informed decisions about material selection for your specific needs.

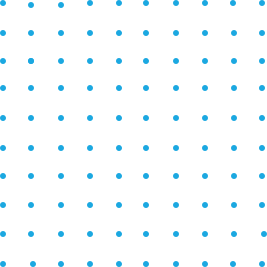
An Expert is just around the corner.
With over 100 years of combined product knowledge and industry experience, we are confident our plastics experts can help you find a solution for your application.
What Are Thermoplastics?
Thermoplastics are polymers that become pliable or moldable at elevated temperatures and harden upon cooling. This heating and cooling cycle can be repeated multiple times without changing the material’s chemical structure, making thermoplastics unique for their recyclability and versatility.
Thermoplastics' molecular structure— chains of repeating units held together by weak intermolecular forces—enables them to be reshaped and reused. Unlike thermosetting plastics (thermosets), which cannot be remolded after the curing process, thermoplastics can be repeatedly melted and reformed, making them an ideal choice for sustainable manufacturing.
Thermoplastics Available at Piedmont Plastics
At Piedmont Plastics, we offer a wide selection of thermoplastics, each with specific properties tailored to different industries. Here are some of the key thermoplastic materials available:
Polycarbonate
Polycarbonate is a high-performance thermoplastic known for its exceptional impact resistance, optical clarity, and heat resistance. Its ability to withstand extreme conditions makes it ideal for safety shields, automotive headlamp lenses, greenhouse panels, and industrial machinery guards. Polycarbonate's ability to maintain structural integrity in both low and high temperatures makes it a favored material in demanding environments.
Technical Specs |
---|
Impact resistance: 250 times stronger than glass |
Heat resistance: Usable up to 135°C (275°F) |
Recyclability: Polycarbonate is recyclable, but it requires careful sorting to remove additives like UV stabilizers. |
Acrylonitrile Butadiene Styrene (ABS)
ABS is known for its toughness, lightweight properties, and ease of processing. It is widely used in automotive components, electronics housings, and consumer products due to its excellent impact resistance and dimensional stability. ABS can withstand mechanical stress without cracking or breaking, making it ideal for structural applications.
Technical Specs |
---|
Tensile strength: 40 MPa (Megapascal) |
Heat deflection temperature: 90-100°C |
Impact strength: Moderately high, ideal for automotive interiors and consumer electronics |
Acrylic
Acrylic, known as polymethyl methacrylate, is a transparent thermoplastic with superior optical clarity. It is often used as a lightweight, shatter-resistant alternative to glass in applications like windows, displays, aquariums, and signage. Acrylic is UV-resistant and retains its clarity over time, making it suitable for outdoor applications.
Technical Specs |
---|
Light transmittance: 92%, which exceeds that of glass |
Impact resistance: 10 times stronger than glass, though less durable than polycarbonate |
Weather resistance: Acrylic is highly resistant to yellowing and maintains clarity under prolonged UV exposure. |
PETG
PETG combines the durability of PET with the flexibility and easy processing of glycol modification. It is commonly used in medical packaging, food containers, and 3D printing applications. PETG is FDA-approved for food contact and is resistant to many chemicals, making it a preferred material for medical devices and consumer packaging.
Technical Specs |
---|
Chemical resistance: Resistant to alcohols, acids, and diluted bases |
Heat resistance: Up to 70°C (158°F) |
Impact resistance: Higher than acrylic but lower than polycarbonate, suitable for moderate-load applications |
Nylon
Nylon is valued for its toughness, flexibility, and excellent abrasion resistance. It is commonly used in automotive components, mechanical gears, and textiles. Nylon’s ability to absorb impact and resist wear makes it ideal for high mechanical strength applications.
Technical Specs |
---|
Tensile strength: Up to 85 MPa |
Heat deflection temperature: Up to 180°C (356°F) in certain grades |
Abrasion resistance: Extremely high, ideal for gears, bearings, and high-wear components |
Advantages and Considerations of Thermoplastics
Advantages:
Thermoplastics provide a range of benefits that make them suitable for various industries.
Recyclability
The ability to be reshaped and reused multiple times without losing mechanical properties makes thermoplastics an environmentally friendly choice. Many thermoplastics, such as PETG and polycarbonate, can be recycled, reducing material waste and supporting sustainable manufacturing practices.
Impact Resistance
Many thermoplastics, including polycarbonate and ABS, offer high impact resistance, making them ideal for applications requiring toughness and durability. Polycarbonate, for example, is 250 times stronger than glass, which makes it an excellent choice for safety applications.
Versatility in Design
Thermoplastics can be molded into complex geometries, allowing creative design freedom. This particularly benefits automotive and consumer goods industries, where lightweight, durable, and intricately shaped components are necessary.
Cost-Efficiency in Production
Thermoplastics are well-suited for high-volume, low-cost manufacturing processes, including injection molding and extrusion. This efficiency helps lower production costs while maintaining excellent precision in part fabrication.
Limitations:
However, there are also limitations to thermoplastics:
Heat Sensitivity
While thermoplastics like polycarbonate offer excellent heat resistance, others may soften or deform at lower temperatures, limiting their use in high-temperature applications. PETG, for instance, begins to lose structural integrity above 70°C.
UV Degradation
Prolonged exposure to UV light can cause certain thermoplastics, such as polycarbonate, to turn yellow or become brittle over time, though UV-resistant coatings can mitigate this issue.
Chemical Sensitivity
Some thermoplastics are more resistant to chemicals than others. Polycarbonate can be degraded by exposure to certain solvents, while PETG and acrylic offer better chemical resistance.
Common Applications of Thermoplastics
Thermoplastics are highly adaptable and find applications across numerous industries:
Construction: PVC (Polyvinyl Chloride) is one of the most common thermoplastics used in construction for pipes, roofing sheets, and window frames due to its durability, chemical resistance, and weatherproofing capabilities.
Automotive: Thermoplastics like ABS and polycarbonate are widely used in automotive components. ABS is commonly found in interior panels, while polycarbonate is used in exterior lighting systems and safety glass alternatives due to its high impact resistance.
Medical and Food Packaging: PETG is extensively used in medical devices, food packaging, and containers due to its chemical resistance, clarity, and sterilization ability. Its compliance with FDA standards makes it suitable for direct food and medical contact.
Electronics: ABS and polycarbonate are frequently used in the electronics industry for housing components, display screens, and protective cases. These materials provide strength, durability, and resistance to heat and impact.
Thermoplastics vs. Thermosets
Thermoplastics are often compared to thermosetting plastics (thermosets) due to their similar usage in manufacturing. However, thermoplastics can be reshaped and reused, whereas thermosets undergo irreversible chemical changes once cured. Thermosets are generally more heat-resistant but lack the flexibility and recyclability of thermoplastics.
This makes thermoplastics ideal for applications requiring frequent reshaping and recyclability, while thermosets are preferred in high-temperature or durable applications like aerospace components.
Environmental Impact and Sustainability
Thermoplastics play a crucial role in sustainable manufacturing. Many thermoplastics, such as PETG and polycarbonate, are recyclable and can be repurposed at the end of their life cycle. By promoting recycled thermoplastics, industries can reduce waste and minimize their environmental footprint.
Thermoplastic processing generates fewer volatile organic compounds (VOCs), making it an eco-friendlier choice for many industries.
Need Further Assistance?
Thermoplastics offer many properties that make them essential materials in today’s industries. Thermoplastics provide the versatility and performance necessary to meet these demands, whether you need high-impact resistance, chemical stability, or optical clarity. From construction to automotive and electronics, our team of experts is ready to help you choose the right thermoplastic for your application.
Learn More
Contact us to learn how we can support your next project with high-quality thermoplastic solutions!
Get In Touch