Driving Innovation in Semiconductor Manufacturing
At Piedmont Plastics, we understand that the semiconductor industry operates incredibly precisely, demanding the utmost precision and cleanliness. Any contamination in the manufacturing process can introduce significant defects in the final products, necessitating strict cleanroom environments.
The production of semiconductors also exposes materials and equipment to extreme temperatures and harsh chemicals used in etching and cleaning processes. This challenging environment requires specialized materials that can withstand these conditions without deteriorating, ensuring the reliability and functionality of the semiconductor devices produced.
Our advanced engineering solutions and high-performance materials are designed to meet these rigorous standards of durability and resistance, supporting the critical needs of the semiconductor industry.

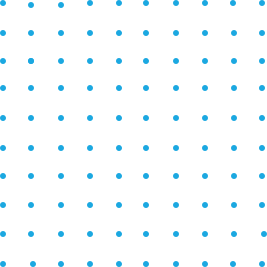
An Expert is just around the corner.
With over 100 years of combined product knowledge and industry experience, we are confident our plastics experts can help you find a solution for your application.
Role of Plastics in Semiconductor Fabrication
In the semiconductor industry, high-performance plastics are gaining popularity over traditional materials like ceramics or quartz. Their flexibility and, most importantly, their cost-effectiveness make them a preferred choice. Plastics such as HDPE, polycarbonate, and polypropylene offer unique advantages, including lower cost, ease of machining, and excellent resistance to the harsh chemicals used in semiconductor manufacturing.
For instance, HDPE is widely used for parts that require strong resistance to acids and contaminants. It also proves its versatility by being ideal for protective surfaces and containers within cleanrooms.
Polycarbonate is utilized not just for its strength and impact resistance but also to demonstrate its adaptability in making protective covers and structural components of semiconductor machinery. In contrast, polypropylene is not just preferred for its chemical resistance, but it also shows its flexibility in wet benches and chemical handling systems.
Key Plastics Used in Semiconductor Manufacturing
In semiconductor manufacturing, the choice of materials is critical due to the precise and demanding nature of the process. Among the plastics utilized, a few stand out for their unique properties and suitability for specific applications within this high-tech industry, which include:
HDPE (High-Density Polyethylene):
Properties: HDPE offers excellent strength and resistance to acids and other chemicals.
Uses: The material is commonly used in fabricating containers, linings, and parts that must resist contamination and degradation.
Advantages: Its resistance to mold and mildew makes it ideal for maintaining the stringent cleanliness required in semiconductor fabrication environments.
Properties: Polycarbonate is known for its high impact strength and clarity.
Uses: It is utilized for protective covers, device test sockets, and structural components of semiconductor machinery.
Advantages: Its ability to be formed and cut on-site allows for precise adaptations, and its resistance to electrical shocks makes it safe for sensitive manufacturing processes.
Properties: Polypropylene exhibits outstanding chemical and acid resistance.
Uses: It is widely used for wet benches, chemical baths, and as parts within the handling systems where harsh chemicals are prevalent.
Advantages: Its durability and economic efficiency support the industry's performance and cost containment needs in rigorous settings.
Advanced High-Performance Plastics
These plastics are specifically engineered to resist extreme temperatures, aggressive chemicals, and mechanical stress, ensuring the reliability and durability of semiconductor manufacturing equipment. Popular materials include:
FEP (Fluorinated Ethylene Propylene):
Characteristics: Highly transparent, resistant to sunlight, soft, and flexible with a lower melting point.
Advantages: Offers excellent chemical resistance and useful low-friction properties.
Typical Applications: Utilized in coating applications that involve exposure to harsh chemicals and detergents, making it ideal for protective coatings in semiconductor environments.
PEEK (Polyether Ether Ketone):
Characteristics: A semicrystalline thermoplastic known for its exceptional mechanical strength and chemical resistance.
Advantages: Maintains stiffness and stability at high temperatures, suitable for continuous use in high-heat environments.
Typical Applications: Used in components that require durability and reliability over long periods, particularly in high-temperature semiconductor manufacturing processes.
PTFE (Polytetrafluoroethylene):
Characteristics: Tough, flexible, with excellent chemical resistance and a very low coefficient of friction.
Advantages: Outstanding thermal properties and electrical insulation capabilities.
Typical Applications: Used for insulation, tubing, and liners in semiconductor fabrication where high resistance to temperatures and chemicals is necessary.
Challenges and Solutions
Integrating plastics into semiconductor manufacturing faces challenges, including ensuring materials withstand extreme processing conditions and maintaining essential purity without contamination. Additionally, the industry has encountered supply shortages, with statistics indicating the fluctuating availability of critical polymer materials impacting production timelines. Research is focused on enhancing plastics' thermal and chemical resistance to address these challenges.
Future advancements will likely involve developing innovative polymer blends that offer superior heat resistance, enhanced mechanical strength, and reduced static accumulation, aiming to increase supply.
Impact of Plastics on Semiconductor Innovation
Plastics offer useful solutions that meet the industry's exacting standards for precision, cleanliness, and resistance to harsh environments. Their unique properties, such as thermal stability, chemical resistance, and electrical insulation, enable the development of more complex and miniaturized semiconductor devices.
The role of plastics in semiconductor applications is expected to grow, driven by continuous advancements in material science that are likely to produce even more durable and economical plastics.
Work With Industry Experts
Piedmont Plastics offers a range of high-performance plastics tailored for the semiconductor industry, meeting the unique demands of conductive, insulating, and heat-resistant properties essential for manufacturing and clean room applications. Our products, including static dissipative PVC, acrylic, and polycarbonate, are ideally suited for environments requiring high-temperature tolerance and purity, such as wafer handling and clean room glazing.
With solutions that replace traditional metal parts and enhance semiconductor production, Piedmont Plastics provides materials like CPVC, specialty polycarbonate sheets, polyester film, acetal, and other advanced polymers.
Learn More
For expert advice on the best materials for your semiconductor applications and to explore our extensive product range, contact us to consult with a plastics expert or get a quote!
Get In Touch