Polycarbonate or PVC?
Polyvinyl Chloride (PVC) and polycarbonate (PC) are the most widely used plastics in various industries. Each material offers unique properties that suit specific functions, from construction and automotive to medical equipment and consumer goods.
This article comprehensively compares these two materials based on their properties, cost, manufacturing processes, and applications.

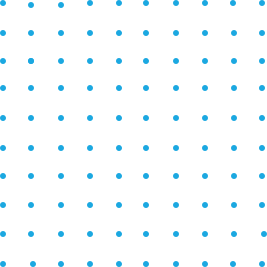
An Expert is just around the corner.
With over 100 years of combined product knowledge and industry experience, we are confident our plastics experts can help you find a solution for your application.
What is PVC?
Polyvinyl Chloride (PVC) is a synthetic plastic polymer made from the polymerization of vinyl chloride monomers. Due to its durability, versatility, and cost-effectiveness, it is the world's third-most manufactured synthetic plastic. PVC comes in two main forms: flexible PVC (Plasticized PVC), which is soft and pliable, and Rigid PVC (Unplasticized PVC or UPVC), which is hard and durable. PVC is commonly used in construction (pipes, window frames), electrical insulation, and packaging.
What is Polycarbonate?
Polycarbonate (PC) is a high-performance, durable thermoplastic made from bisphenol A (BPA) and phosgene. Known for its exceptional impact resistance and optical clarity, polycarbonate is often considered "unbreakable" in many applications. It is significantly stronger than glass and acrylic plastic and has high thermal stability, making it a preferred material for safety equipment, automotive components, and electronic devices.
Comparison of Key Properties
Here is a guide to how PVC and polycarbonate compare to each other:
PVC
Strength and Durability:
PVC offers good mechanical strength and toughness. Rigid PVC is highly resistant to impact and abrasion, making it suitable for piping and construction applications. However, flexible PVC provides more flexibility and is less prone to breaking.
Clarity and Optical Properties:
Rigid PVC can be semi-transparent, but its optical clarity is not as high as polycarbonate. Over time, it may turn yellow when exposed to sunlight without UV stabilizers.
Heat Resistance and Stability:
PVC has lower heat resistance and can deform under high temperatures. It is not recommended for applications requiring exposure to extreme heat.
Chemical Resistance:
PVC is highly resistant to many chemicals, acids, alkalis, and salts. This makes it ideal for industrial applications where exposure to harsh chemicals is common.
Costs and Pricing:
As a commodity material with established specifications, PVC is widely available and affordable.
Ease of Fabrication:
It can be easily cut, welded, molded, and shaped into various forms and fittings. Both rigid and flexible PVC can be machined to tight tolerances and are easily thermoformed, making PVC versatile for different manufacturing processes.
Recyclability:
It is 100% recyclable through mechanical (grinding, remelting, and remolding) and chemical (pyrolysis or hydrolysis) recycling methods. However, the presence of additives can complicate the recycling process.
Polycarbonate
Strength and Durability: Polycarbonate has exceptional impact resistance, making it over 200 times stronger than glass and 30 times stronger than acrylic at the same thickness. This high level of resistance to breakage makes it an ideal choice for applications requiring durability and safety, such as eyewear and safety shields.
Clarity and Optical Properties:
It exhibits excellent optical clarity and allows light transmission better than glass. It is commonly used in applications like lenses, optical devices, and greenhouse panels. However, without UV-resistant coatings, polycarbonate can also yellow over time.
Heat Resistance and Stability:
This material offers high thermal resistance, with a maximum service temperature higher than many other clear plastics. It maintains stability and does not deform under high heat, making it suitable for applications like medical devices and automotive components.
Chemical Resistance:
When coated, it resists many aggressive chemicals at room temperature. However, its resistance decreases with increased temperatures.
Costs and Pricing:
The complex manufacturing process and high specialization make polycarbonate a higher-cost material.
Ease of Fabrication:
This material exhibits excellent machinability and can be easily thermoformed and molded. However, its softness makes it more susceptible to scratching and requires protective coatings for specific applications.
Recyclability:
Polycarbonate is fully recyclable. The process involves sorting, shredding, and washing to remove impurities and color contamination before granulating it for reuse. Recycled polycarbonate also retains much of the strength and clarity of virgin material.
Applications and Use Cases
PVC and polycarbonate have distinct applications based on their properties. In construction, PVC is extensively used for pipes, window frames, roof linings, and cladding due to its cost-effectiveness, stability, and chemical resistance.
Polycarbonate, with its high impact strength and optical clarity, is preferred for skylights, greenhouse panels, and security glazing. Polycarbonate is used for headlight lenses, sunroofs, and various interior and exterior components, requiring durability and transparency in the automotive and transportation sectors. At the same time, PVC is favored for cable insulation, hoses, and seals due to its flexibility and chemical resistance.
In the medical field, polycarbonate is the material of choice for face shields, blood reservoirs, drug delivery systems, and safety eyewear, thanks to its transparency and impact resistance. PVC is also used in medical settings, but more commonly for gloves, aprons, and protective barriers where flexibility and chemical resistance are crucial. In the consumer goods sector, PVC is often used for flooring, vinyl records, and various household items, while polycarbonate is found in eyewear, electronic devices, reusable containers, and outdoor equipment.
Advantages and Disadvantages
PVC is known for its cost-effectiveness and versatility, making it a popular choice for various applications. It offers high chemical resistance and is suitable for both rigid and flexible uses. However, PVC has lower heat stability and can yellow over time without UV stabilizers. It also poses environmental concerns due to releasing toxic chlorine fumes when burned.
Polycarbonate, on the other hand, offers unmatched impact resistance, optical clarity, and thermal stability, making it ideal for safety, medical, automotive, and high-performance applications. Despite its high cost, polycarbonate is fully recyclable and retains much of its original quality. However, it is more susceptible to scratching unless coated, and its price can limit budget-sensitive projects.
Choosing Between PVC and Polycarbonate
Both PVC and polycarbonate have unique strengths. PVC's affordability and versatility make it perfect for a wide range of uses, while polycarbonate’s unbeatable strength, clarity, and thermal resistance suit more demanding environments.
At Piedmont Plastics, we understand that choosing the right material can make all the difference to your project’s success. Contact us to discuss your specific needs, and let our experts guide you to the best solution that balances performance, cost, and sustainability.
How We Can Help
Unsure about which material to select? Let’s work together to bring your project to life with the right plastic!
Contact Us