Everyday Uses for Plastic Tubes
Plastic tubes are indispensable across many industries, providing solutions for fluid flow, structural support, and insulation. Whether in healthcare, automotive, or industrial applications, plastic tubing offers unparalleled versatility.
In this guide, we’ll explore the applications, advantages, and material options for plastic tubes and detail how Piedmont Plastics’ custom solutions can help meet your project’s unique requirements.

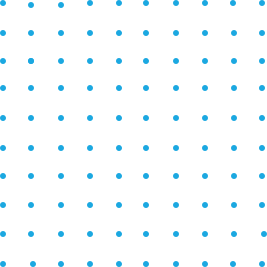
An Expert is just around the corner.
With over 100 years of combined product knowledge and industry experience, we are confident our plastics experts can help you find a solution for your application.
Important Applications for Plastic Tubes
Plastic tubes play a vital role in numerous industries, enabling efficient and safe operations across various applications:
Medical and Pharmaceutical: Plastic tubing is essential in the medical field for fluid transfer in IV lines, catheters, and diagnostic equipment. Medical-grade tubes must be chemically resistant and biocompatible, ensuring they remain safe for patients.
Industrial and Automotive: Industries such as automotive manufacturing use plastic tubing for pneumatic, hydraulic, and fuel systems. Withstanding high pressure, chemical exposure, and fluctuating temperatures, plastic tubes are ideal for harsh industrial settings.
Food and Beverage: FDA-compliant plastic tubing is common in food and beverage production, handling everything from water to food-grade oils. These tubes must resist contamination and maintain purity, making plastic a preferred material for transferring consumable liquids.
Construction and HVAC: Construction sites rely on plastic tubing for drainage, insulation, and cable protection. HVAC systems also utilize plastic tubes to manage air flow and protect electrical components, leveraging the material’s resilience and flexibility.
Types of Plastic Materials for Tubing
Plastic tubing is available in various materials, each offering unique characteristics to suit specific applications. Here are some commonly used plastics in tubing, along with their advantages and common uses:
ABS (Acrylonitrile Butadiene Styrene): ABS tubing is known for its impact resistance and durability. It is used in applications with critical structural integrity, such as protective casings and housings.
Polyethylene (PE): Lightweight and inert, PE is popular for laboratory and food-grade applications. It is highly resistant to chemicals and moisture, making it suitable for environments that require safe, inert materials.
PTFE (Polytetrafluoroethylene): With excellent chemical and temperature resistance, PTFE (often known by its brand name, Teflon®) is ideal for handling aggressive chemicals and high temperatures. PTFE is commonly used in industrial settings where tubes encounter harsh solvents and elevated heat levels.
PVC (Polyvinyl Chloride): PVC offers versatility and affordability. Available in rigid or flexible forms, PVC tubing is used in construction, plumbing, and general fluid transfer applications due to its resistance to abrasion, corrosion, and a wide range of chemicals.
Polyurethane: Combining flexibility with strength, polyurethane tubing is used in fuel lines and industrial hoses. Its resistance to chemicals like gasoline and oils makes it suitable for demanding automotive and industrial applications.
Comparing Plastic Tubing Materials
Choosing the right tubing material requires understanding each option's unique properties and potential trade-offs. Here’s a comparison of popular materials to help you determine the best fit for your needs:
Material | Key Benefits | Applications | Limitations |
---|---|---|---|
ABS | High impact resistance, good dimensional stability | Protective casings, industrial housings | Not suitable for high temperatures or strong chemicals |
Polyethylene (PE) | Inexpensive, good chemical resistance, lightweight | Food & beverage, laboratory tubing | Lower temperature tolerance |
PTFE | High chemical resistance, withstands high temperatures (-454°F to 500°F), low friction | Industrial, chemical processing | Costlier, not easily weldable |
PVC | Affordable, flexible, or rigid options, broad chemical resistance | Plumbing, construction, food & beverage | Limited temperature range (up to 165°F) |
Polyurethane | High flexibility, abrasion resistance, resistance to oils and fuels | Fuel lines, hoses, automotive applications | Prone to degradation in humid environments (ester-based) |
Polypropylene | Lightweight, good chemical resistance, weldable | Packaging, lab containers, structural tubing | Limited thermal stability, lower strength |
Advantages of Plastic Tubes Over Alternatives
Plastic tubes offer significant benefits over traditional materials like metal, especially in environments demanding durability and flexibility. Here are just a few:
Lightweight: Plastic tubes are much lighter than metal, making them easier to transport, handle, and install, which reduces project costs.
Cost-Effective: Plastic tubing is more economical than metal and other alternatives, offering a high-performance option without the price tag.
High Durability: Resistant to corrosion, impact, and chemical degradation, plastic tubing can withstand challenging conditions, making it a long-lasting choice.
Flexibility: Many plastics offer high flexibility, making plastic tubing easy to maneuver in tight spaces or around obstacles, which is especially beneficial in complex installations.
Low Maintenance: Plastic tubing requires less upkeep than metal, as it is naturally resistant to rust, corrosion, and chemical damage, decreasing long-term maintenance costs.
Items To Consider
The specific demands of the intended application should guide the choice of plastic tubing. First, consider the temperature and pressure ratings to ensure that the tubing material can withstand the conditions it will encounter.
Next, assess chemical compatibility by confirming that the material resists any chemicals it will contact, particularly in industrial, laboratory, and food settings.
For applications requiring medical or food-grade standards, ensure the material follows FDA or other relevant standards. Finally, evaluate the tubing’s performance specifications, including dielectric properties, strength, and flexibility, especially for electrical, structural, or high-stress uses.
Expertise in Custom Plastic Tubing Solutions
Piedmont Plastics is a trusted provider of plastic tubing solutions, offering an extensive selection of materials to meet the unique requirements of each industry. Our products include ABS, polyethylene, PTFE, PVC, and polyurethane, with each material optimized for specific applications. We offer a full range of customization services, including cut-to-size options, fabrication, and compliance with industry standards like FDA, RoHS, and more.
Piedmont Plastics is committed to quality and precision. We ensure that each tubing solution meets the highest standards of durability, safety, and efficiency. From the medical field to food and beverage applications, we offer customized solutions tailored to enhance performance across various industries.
Let's Work Together
Plastic tubes are essential in modern industry, providing durability, adaptability, and cost-effectiveness. Whether for industrial systems, food-grade tubing, or flexible automotive applications, Piedmont Plastics is here to help you make the best choice in plastic tubing.
Contact An Expert