The Hidden Importance of Plastic Covers and Caps
Plastic covers and caps may seem like small, insignificant components, but they serve an essential purpose across a variety of industries. They help seal containers, prevent contamination, and enhance safety during transportation and storage. Whether used in industrial machinery, automotive parts, food packaging, or pharmaceuticals, these simple tools play a critical role in ensuring product integrity, hygiene, and protection.
We come across plastic caps and covers every day without even realizing their importance. The twist-off cap on a water bottle, the child-resistant lid on a medicine container, or the protective cover on electrical wiring all serve specific functions that keep products safe and usable. In industrial and manufacturing settings, these components become even more crucial, preventing metal corrosion, protecting delicate machinery, and ensuring compliance with safety regulations.
Knowing the different types of plastic covers and caps, how they are manufactured, and their various applications allows industries to choose the right solutions for their needs. This article explores the many uses of plastic caps and covers, the materials used in their production, and the benefits they bring to a wide range of industries.

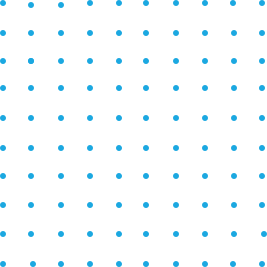
An Expert is just around the corner.
With over 100 years of combined product knowledge and industry experience, we are confident our plastics experts can help you find a solution for your application.
Types of Plastic Covers and Caps
Plastic covers and caps come in many forms, each designed for a specific purpose. Some are used to securely seal containers, while others provide protection against damage, contamination, or workplace hazards.
The two most common types are threaded and non-threaded caps, but there are also specialized options for various industrial and commercial applications. Learn more about each one:
Threaded Caps | These caps screw onto containers, creating a strong and dependable seal. They are commonly used on bottles, jars, and tubes to keep liquids, powders, and creams fresh while preventing leaks and contamination. |
---|---|
Non-Threaded Caps | Instead of screwing on, these caps snap or press into place. They are often used for sealing paint cans, industrial drums, and storage pails, relying on a tight friction fit rather than threads. |
Tapered Caps and Plugs | Designed to fit both inside and over an opening, these versatile caps protect exposed threads, metal tubing, and pipe ends. They are widely used in industrial and automotive settings to prevent dust, moisture, and damage. |
Tamper-Evident Caps | These caps ensure that a product has not been opened or altered before reaching the customer. Common in food and pharmaceuticals, they feature a breakable ring or band that separates when the cap is first opened, providing a visible sign of tampering. |
Utility and Protection Caps | These caps are used to cover exposed threads, sharp edges, and open-ended pipes, enhancing safety and durability. They are often found in transportation, construction, and industrial applications where they help protect both workers and equipment. |
Specialized Caps | Some caps are designed for specific applications. For example, fuel injector caps prevent contamination in automotive engines, while driveshaft protection caps safeguard machinery parts during transport and storage. |
Applications and Uses Across Industries
Plastic caps and covers play a vital role in a wide range of industries, offering protection, safety, and durability. Whether sealing a product, preventing contamination, or safeguarding equipment, these small components have a big impact.
In the packaging industry, plastic caps are essential for sealing bottles, jars, tubes, and drums. They help keep food, beverages, and personal care products fresh while preventing leaks and contamination. Screw-on caps for beverage bottles, flip-top caps for shampoos, and specialized closures for cosmetics all serve to preserve product quality. In pharmaceuticals and food packaging, tamper-evident and child-resistant caps provide an added layer of security, guaranteeing consumer safety and compliance with industry regulations.
Industrial applications rely on plastic caps for equipment protection and workplace safety. In hydraulic systems, caps prevent dust and debris from entering sensitive components, reducing the risk of system failure. In construction, exposed scaffolding and metal tubing are fitted with end caps to prevent corrosion and protect workers from sharp edges. During transportation and storage, threaded caps and plugs keep metal components clean, preventing damage and safeguarding parts arrive in perfect condition.
The automotive industry also depends on plastic caps for protecting vital components. Driveshaft caps shield moving parts from dust and debris, while fuel injector caps prevent contamination inside critical engine systems. Plastic plugs are often used during vehicle manufacturing to seal off engine parts, ensuring they stay clean and functional throughout assembly and transport.
In the medical and pharmaceutical sectors, plastic caps play a fundamental role in supporting hygiene and safety. Child-resistant closures prevent accidental ingestion of medications, while sterile sealing caps protect medical supplies from contamination. In laboratories, precision-sealed caps are used on test tubes and vials to make certain the integrity of samples.
How Plastic Caps and Covers Are Manufactured
The manufacturing of plastic caps and covers is just as crucial as their design, as it determines their durability, flexibility, and suitability for different applications. Two primary methods are used to produce these components: injection molding and dip molding. The choice of method depends on the type of cap being made, its required properties, and the material used.
Equally important as the manufacturing method is the choice of material, which affects the cap's flexibility, durability, and resistance to environmental factors. Common materials used include:
Low-Density Polyethylene (LDPE): Known for its lightweight and impact-resistant properties, LDPE is commonly used for general-purpose caps and plugs. It offers flexibility, making it easy to apply and remove while keeping a secure fit.
High-Density Polyethylene (HDPE): Stronger and more rigid than LDPE, HDPE provides excellent chemical resistance and durability. This makes it ideal for heavy-duty industrial applications, such as chemical storage and hydraulic system protection.
Polyvinyl Chloride (PVC): A high-density material that resists impact and weathering, PVC is widely used in electrical and outdoor applications. Its strength and non-conductive properties make it a popular choice for protective caps in wiring and construction.
Polypropylene (PP): Cost-effective and resistant to stress cracking, polypropylene is a tough material that keeps its shape under pressure. It is widely used in packaging applications, particularly for bottle caps and container lids.
Nylon: This rigid, high-strength material is known for its abrasion resistance and durability. It is often used for threaded sealing caps and industrial locking plugs that require a secure and long-lasting fit.
The Benefits of Using Plastic Caps and Covers
One of the greatest advantages of plastic caps and covers is their ability to protect products from damage and contamination. Whether sealing off a bottle of liquid, covering an exposed pipe, or protecting sensitive engine components, these small but crucial pieces help maintain product integrity and functionality.
Safety is another major benefit. In industrial settings, plastic caps reduce the risk of workplace injuries by covering sharp edges and preventing exposure to hazardous chemicals. Tamper-evident and child-resistant caps further enhance consumer safety, ensuring that products reach customers in their intended, untampered state.
Durability is a major factor as well. Plastic caps are designed to withstand harsh environments, including extreme temperatures, moisture, and physical impact. High-quality materials like HDPE and nylon provide resistance to chemicals, UV exposure, and wear and tear, making these caps long-lasting and reliable.
Cost-effectiveness also makes plastic caps and covers a preferred choice. Compared to metal alternatives, plastic options are lightweight, easy to produce, and affordable. Their adaptability allows manufacturers to create customized designs for specific applications without significant added costs.
Need Additional Information?
Though often overlooked, plastic caps and covers play an important role in numerous industries. Their ability to seal, protect, and enhance safety makes them indispensable in packaging, manufacturing, automotive, and industrial applications.
If you need to buy plastic material for your cap or cover, contact our team!
Receive Specialized Solutions
Get in touch with our sales experts today to find out more about how we can assist with your next project!
Learn More