PETG (polyethylene terephthalate glycol) is a transparent sheet material made from thermoplastic polyester. It is known for its superior clarity and light transmission combined with a high gloss surface finish. Therefore, it is considered one of the most popular forms of plastic sheet around.
The polyethylene terephthalate component of PETG often appears in plastic beverage bottles and food products. The addition of glycol provides enhanced durability and strength. It also adds to PETG’s overall impact resistance and ability to withstand high temperatures.
PETG sheet is a popular material for thermoforming because it uses little energy, has short production cycles, has high draw ratios, and makes good mold copies without being pre-dried. However, even at low temperatures, PETG sheets can take a lot of abuse and are approved for use in food contact applications.
PETG can also be fabricated using various techniques such as vacuum forming, hot and cold line bending, drilling, and milling. In addition, PETG sheet can be cut to size easily for your precise manufacturing needs.

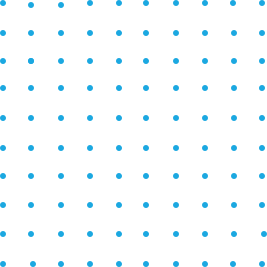
An Expert is just around the corner.
With over 100 years of combined product knowledge and industry experience, we are confident our plastics experts can help you find a solution for your application.
What Is PETG Used For?
PETG is used in many different fields because it can handle heat, impact, and solvents. Here are a few industries that make good use of PETG.
Indoor and Outdoor Signage and Displays
Because PETG sheets are easy to screen-print, it’s a popular choice for the advertising and signage industries. Its versatility, durability, and impact resistance make PETG perfect for displays, sign making, glazing, and protective screens. In addition, UV-resistant grades of PETG allow outdoor uses that require protection from aging due to sunlight.
Medical Applications
Because of its rigid structure and ability to withstand the severe sterilization process, PETG is ideal for producing medical implants and packaging material for different medical devices and pharmaceutical products.
Machine Protection
PETG is a perfect material choice for producing parts that require both flexibility and shock resistance, making it a quality material for fabricating machine guards or protections. In addition, thanks to flexible forming properties and its resulting hardness, PETG machine protection products can last for years. For these reasons, it’s considered a good alternative to polycarbonate materials when making guards for the food processing industry.
PETG also meets ANSI Z87.1 requirements for occupational and educational personal eye protection devices.
Beverage Containers
PETG is often used to make containers for water, soda, cooking oils, and food and drink storage containers that meet FDA standards. PETG is highly resistant to chemicals, making it ideal for companies to use for holding beverages and other liquids. Its light weight also means it costs less to ship than other container materials.
PETG is also recyclable, making it a good choice for manufacturers who want to promote green policies.
Differences Between PETG and Acrylic
Acrylic may be a viable option for many of the applications mentioned above. But how does acrylic compare to PETG in a head-to-head comparison?
Most manufacturing needs come down to strength, clarity, maintenance, and cost.
Strength
Both acrylic and PETG are strong and resilient. Acrylic is a very dense and rigid material, but when it experiences excessive impact or force, it can shatter or crack, resulting in sharp, potentially dangerous edges.
By comparison, PETG is impact resistant and won’t shatter like acrylic. Because it’s about five times stronger than acrylic, PETG is ideal for displays in high-traffic areas. It’s also a better choice for packaging as it will experience minor damage during shipping.
Clarity
In this case, acrylic comes out ahead with its excellent optical clarity. However, where acrylic can substitute for glass in some applications, PETG carries a slight blue/green hue.
Acrylic offers a variety of color options and can run from fully clear transparency to different stages of opaqueness. PETG color options are limited and usually only available in clear gloss or clear matte finishes.
Maintenance
Both acrylic and PETG are simple to clean, often requiring soap and water. For long-term use, acrylic may edge out PETG, but if it is a component or piece of signage that gets replaced periodically, that may not be much of a factor in the end, and PETG’s superior strength may win out.
PETG at Piedmont Plastics
Piedmont Plastics works with industry-leading suppliers like Plaskolite, Inc. and Primex Plastics to offer PETG sheet in various formulations and gauges for a wide range of applications.
Piedmont offers various sizes of PETG, including a 48” x 96” standard sheet size, and gauges from .020” to .236”. Contact our materials expert team today to help you find the best PETG sheet for your manufacturing needs.