Lightweight Plastics in Aerospace and Automotive
As industries across the globe strive to improve efficiency, reduce operational costs, and adhere to increasing environmental standards, lightweight materials are becoming a crucial factor in innovation within aerospace and automotive engineering. Due to their strength and durability, traditional materials such as aluminum, steel, and titanium have long been used in these industries.
However, the introduction and evolution of high-performance plastics have significantly changed the landscape. These advanced materials now offer comparable strength and superior flexibility while reducing weight, increasing fuel efficiency, and lowering emissions.
As the demand for lightweight alternatives continues to grow, engineers and designers are turning to plastics to replace conventional materials in structural, mechanical, and aesthetic applications. In this article, we explore the latest innovations in lightweight plastics, their expanding role in these industries, and how manufacturers are leveraging these materials.

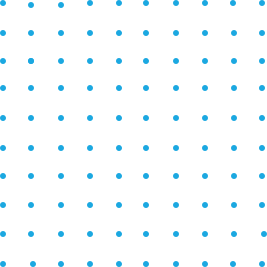
An Expert is just around the corner.
With over 100 years of combined product knowledge and industry experience, we are confident our plastics experts can help you find a solution for your application.
The Game-Changing Science Behind Lightweight Plastics
The concept of lightweighting is centered around the idea of reducing the mass of components while maintaining or enhancing their mechanical properties, durability, and structural integrity. Advances in material science have allowed for the development of thermoplastics and composite materials that offer a unique combination of high strength, low density, and excellent chemical resistance. These materials are designed to withstand extreme temperatures, impact forces, and prolonged wear, rendering them suitable for aerospace and automotive applications.
Plastics offer a level of design flexibility that metals cannot achieve. Engineers can mold, extrude, or 3D print plastic components into complex geometries that optimize aerodynamics and reduce drag. Additionally, these materials exhibit corrosion resistance, reducing the need for expensive coatings and treatments required for metal parts.
By incorporating reinforced fibers such as carbon or glass, engineers can ensure the strength of plastic components rivals that of metal counterparts, enhancing their viability for high-performance applications.
High-Performance Plastics Driving Lightweight Innovations
Ultra-High Molecular Weight Polyethylene (UHMW)
UHMW is a high-strength, low-cost plastic that provides outstanding impact and abrasion resistance. It is particularly beneficial in aerospace applications where components are subject to high levels of stress and require exceptional durability. UHMW also features low moisture absorption and excellent wear resistance, which means it is ideal for parts that must maintain their integrity across varying environmental conditions.
Part of the thermoplastic polyetherimide (PEI) family, Ultem is a highly versatile material known for its superior mechanical, thermal, and electrical properties. It offers remarkable dimensional stability, inherent flame resistance, and chemical resistance, making it one of the most sought-after materials in the aerospace and automotive industries. Ultem's resistance to stress and cracking when exposed to fuels, solvents, and industrial fluids further increases its usability in high-performance applications.
Nylon is widely used as a lightweight alternative to metals in structural applications. It is a high-strength thermoplastic that exhibits excellent temperature resistance, chemical compatibility, and wear resistance. Due to its ease of machining and cost-effectiveness, it is a common choice for replacing metal components in gears, bushings, and mechanical fasteners.
Also known as PTFE, Teflon is recognized for its exceptional operating temperature range, low friction coefficient, and superior chemical resistance. These properties position it as a preferred material for aerospace seals, gaskets, and high-performance coatings. PTFE also boasts high electrical insulation properties, and it is ideal for electronic components used in both automotive and aerospace applications.
PEEK is one of the most widely used high-performance plastics in the aerospace and automotive industries due to its ability to endure extreme environmental conditions. This polymer is highly resistant to thermal degradation, harsh chemicals, and mechanical stress. It also exhibits superior creep resistance and can withstand prolonged exposure to high-pressure steam and water. With these properties, PEEK is commonly found in aircraft interiors, under-the-hood automotive applications, and structural components requiring longevity and strength.
Manufacturing Techniques for Lightweight Plastics
The demand for lightweight materials has driven innovation in manufacturing techniques that optimize material properties while minimizing waste. Modern manufacturing methods include:
Injection Molding
This technique allows for the efficient production of complex plastic components with minimal material waste, leading to cost savings and improved structural integrity.
Foaming and Composites
The introduction of foaming agents and fiber reinforcements, such as carbon and glass fibers, enhances the strength-to-weight ratio of plastic parts.
Thermoforming and Vacuum Forming
These processes enable the production of durable, lightweight components used in aircraft interiors and automotive panels.
Pressure Molding
This method ensures that plastic materials achieve uniform strength and density, which is critical for structural applications in aerospace and automotive industries.
What Does The Future Hold?
As industries continue to prioritize efficiency and sustainability, the role of plastics in aerospace and automotive applications will only expand. Advancements in nanocomposites, biodegradable plastics, and shape-memory polymers are paving the way for next-generation lightweight materials. Additionally, the shift towards electric vehicles (EVs) and more fuel-efficient aircraft will further drive demand for materials that can optimize energy consumption without compromising performance.
Plastics will also play a critical role in reducing the environmental footprint of manufacturing processes. Many thermoplastics are recyclable and can be reprocessed with minimal energy consumption.
Let’s Work Together!
At Piedmont Plastics, we remain at the forefront of providing innovative plastic solutions tailored to the needs of modern aerospace and automotive engineering. As the industry continues to evolve, we are committed to offering cutting-edge materials and expertise to help manufacturers push the boundaries of what is possible.
Connect With The Experts
For more information on how our lightweight plastic solutions can improve your projects, contact our team!
Get In Touch