A Guide to Selecting the Right Plastic Material
Polyethylene (PE) is a hugely popular manufacturing material for many reasons. It’s easily machinable, compatible with other materials, and relatively inexpensive. Consumer goods, medical equipment, and industrial, fuel, and chemical use, such as tanks and pipes, all use PE extensively.
PE can come in several forms, but the most popular types are high-density polyethylene (HDPE) and low-density polyethylene (LDPE). Both are extremely useful to various industries, but they’re not interchangeable.
Here’s what you need to know about selecting the right kind of polyethylene for your upcoming project.

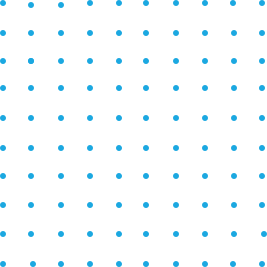
An Expert is just around the corner.
With over 100 years of combined product knowledge and industry experience, we are confident our plastics experts can help you find a solution for your application.
All About High-Density Polyethylene (HDPE)
HDPE is a very strong polyethylene with excellent tensile strength, stiffness, and impact resistance, thanks to its molecules’ proximity. In addition to being UV-resistant, HDPE is chemically resistant, strong, and a very versatile material that is simple to work with.
Due to its malleability and dimensional stability, HDPE is frequently used in outdoor furniture, playground equipment, and construction. In addition, HDPE can be found in numerous consumer products like food and beverage bottles, cutting boards, and toys, and is also employed in industrial applications like pipe flanges and chemical tanks.
One of the most significant benefits of HDPE is its ability to be recycled and reused. Because HDPE tends to be as adaptable and weldable as new or “virgin” HDPE, recycled high-density polyethylene is an excellent choice of material for those wishing to lower their environmental impact.
Some downsides of HDPE include its susceptibility to stress cracking under high pressure and its poor to moderate heat resistance. In addition, as HDPE is prone to shrinkage when molded, CNC machining and additive manufacturing are the best applications for it.
Melting Point | Water Absorption | Tensile Strength | Tensile Elongation |
---|---|---|---|
275°F (135°C) | 0.10% | 4,000 psi | 600 psi |
All About Low-Density Polyethylene (LDPE)
LDPE is a branching variety of polyethylene, so its molecules are arranged more loosely and allow for a lower density than other linear polyethylene materials like HDPE. At the same time, LDPE is a strong, robust material suitable for many purposes. It boasts excellent impact resistance, stain resistance, electrical insulating properties, and water resistance. LDPE is also transparent and good for light reflection.
Typical LDPE consumer components include grocery bags, plastic film or wraps, flexible packaging material, and food and beverage containers. Moreover, LDPE is a common material used to manufacture orthotics and prosthetics.
As a benefit of low-density polyethylene’s relatively low heat resistance and melting point, it is an ideal material for heat sealing. This feature also makes it an excellent material choice for injection molding, allowing it to serve various manufacturing needs.
In addition to lower heat resistance, LDPE has some limitations that manufacturers should know. For instance, it is highly permeable to gases like carbon dioxide and more prone to stress cracking than HDPE. Also, due to its extreme flammability, LDPE’s employment in high-temperature applications is severely constrained.
Melting Point | Water Absorption | Tensile Strength | Tensile Elongation |
---|---|---|---|
239°F (115°C) | 0.10% | 1,400 psi | 500 psi |
HDPE vs. LDPE
Both materials are highly durable, weldable, impact, chemical resistant in addition to malleable and manufacturable. HDPE is a more rigid material than LDPE, but both are tough and wear-resistant. Finally, whereas LDPE is a transparent, branching variant of PE, HDPE has a linear structure and is opaque.
While both injection molding and additive manufacturing can process LDPE and HDPE, LDPE is best suited for injection molding. At the same time, HDPE can be machined utilizing CNC technology to assist in reaching precise tolerances. Manufacturers should consider carefully which material is most appropriate for a given project. The materials experts at Piedmont Plastics can provide more information and help you determine the best materials for your manufacturing challenges.
LDPE and HDPE At Piedmont Plastics
Piedmont Plastics’ teams of skilled specialists are prepared to offer you the applications-specific solutions you want.
For more information on how high and low-density polyethylene can be the best option for your needs and how we can support you and your products, get in touch with us today.