Modern construction practices increasingly rely on plastics to address issues such as corrosion, handling challenges, and long-term maintenance costs. Whether used for rebar chairs in reinforced concrete, formwork for walls and slabs, or channel drains for water management, plastics such as high-density polyethylene (HDPE) and polypropylene bring unique advantages. These include lightweight handling, resistance to environmental factors, and cost-efficiency.
Below is an in-depth look at how these plastic components are transforming today’s building processes, with real-life examples of successful projects that have used plastic materials.

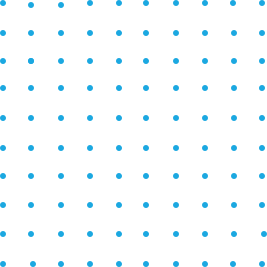
An Expert is just around the corner.
With over 100 years of combined product knowledge and industry experience, we are confident our plastics experts can help you find a solution for your application.
Why Plastics Matter in Construction
Plastics have become increasingly important in construction due to their practicality. Their lightweight nature and resistance to chemical and environmental degradation make them a reliable choice. Advances in polymer technology have made modern construction-grade plastics durable enough to manage significant loads, withstand thermal fluctuations, and endure long-term outdoor exposure. This versatility positions plastics as a practical and dependable alternative to traditional steel, wood, and concrete materials.
Another key advantage of plastics is their ability to reduce maintenance needs. Unlike metal, which can rust, or wood, which is prone to rotting, plastics stay unaffected by moisture and many chemicals. Although the upfront cost of plastics may be higher than some materials, the long-term cost savings from reduced repairs and replacements often outweigh the initial investment. Plastics are also lighter and easier to handle, accelerating installation and lowering labor costs.
Key Reasons Why Plastics Excel in Construction
Durability
Plastics resist rust, rot, and chemical corrosion, even in challenging environments.
Lightweight
Plastics are easy to transport, handle, and install, reducing labor and shipping costs.
Versatility
Plastics adapt to diverse applications, from rebar chairs and formwork to drainage systems.
Low Maintenance
They require minimal upkeep, offering significant cost savings over the life of a project.
Efficiency
They simplify project timelines by speeding up setup and reducing delays caused by material failures.
Rebar Chairs: Reinforcement Done Right
Rebar chairs, sometimes referred to as rebar spacers, are support tools used in construction to hold reinforcing bars (rebar) in place before and during the pouring of concrete. They ensure that the rebar is properly positioned within the concrete slab or structure, maintaining the required distance (or "cover") from the formwork or surface. Traditional rebar chairs were often made of steel, which can introduce problems such as rust stains, potential weakening of the concrete cover, and added installation complexity.
Plastic rebar chairs solve many of these challenges. They do not rust or corrode when exposed to moisture and chemicals, making them suitable for longer service life. They are also significantly lighter than metal rebar supports, simplifying positioning before and during the pour.
Many plastic chairs come with snap on designs that allow them to grip reinforcing bars securely without separate binding wires. This reduces setup time and decreases the chance of accidental displacement. From residential foundations to large bridges and commercial infrastructures, plastic rebar chairs play a critical role in ensuring the integrity and safety of reinforced concrete.
Plastic Formwork: Efficient and Sustainable Molding
Plastic formwork uses panels and modular systems made from polymers such as HDPE or polypropylene to shape fresh concrete. These systems are assembled to create the mold, with concrete poured into the enclosed form. Once the concrete has been cured, the plastic panels can be removed, cleaned, and reused multiple times. Wood-based formwork can only withstand a limited number of uses before it degrades, absorbs water, or warps, making plastic a more durable alternative.
Beyond longevity, plastic formwork panels are exceptionally lightweight compared to timber or steel forms. This reduces the need for workers to transport and install them while minimizing reliance on heavy machinery for movement and positioning. The panels also resist corrosion and rot, remaining stable when exposed to weather or chemical environments.
Plastic formwork often provides a uniform, smooth finish, eliminating the need for extensive surface treatments after form removal. By storing the panels correctly and cleaning them between pours, contractors can maximize the number of reuse cycles, ultimately reducing overall material costs.
Plastic Drainage Systems: Channel Drains and Beyond
Channel drains made from plastic are an increasingly popular solution for effective water management in commercial and residential settings. They direct surface water away from critical areas in sites such as driveways, pool decks, and industrial facilities. While older drainage systems typically rely on concrete or metal components, plastic drainage channels offer significant advantages that make them suitable for various applications.
HDPE and polypropylene drainage systems resist chemicals, oils, and solvents, making them ideal for contaminated water disposal or areas exposed to harsh cleaning agents. Their smooth internal surfaces support high flow rates, minimizing debris buildup and simplifying long-term maintenance.
Because of the lightweight nature of plastic, installation crews can easily transport channel sections, adjust positioning on-site, and secure fittings without specialized machinery. Plastic drainage systems are also available in modular segments, with optional grates in different materials and styles. This flexibility ensures that the channels can be adapted to accommodate loads ranging from pedestrian walkways to high-traffic driveways and parking lots.
Cost Analysis and Long-Term Value
While the upfront cost of plastic components may be higher than traditional materials like metal or wood, their long-term benefits often outweigh this initial expense. Plastics resist rust, rot, and chemical damage, reducing maintenance and replacement needs. Products like plastic rebar chairs require no corrosion-related inspections, and plastic formwork offers multiple reuse cycles, far surpassing wooden alternatives.
Their lightweight and modular designs make plastic components easier to handle and install, saving time and labor costs. Plastics are cost-effective and durable for moderate to light loads in residential, commercial, or light industrial settings, making them a smart investment.
Key benefits include:
Lower maintenance and replacement costs
Reusability over multiple projects
Faster installation, reducing labor expenses
Long-term savings that offset higher upfront costs
Design Flexibility and Aesthetic Considerations
Plastics are highly moldable, enabling them to be formed into complex shapes and produced in a range of colors. This customizability is valuable when architectural or landscaping needs call for intricate or visually appealing finishes.
Formwork panels can be designed with minimal seams, creating crisp edges and consistent surfaces in decorative concrete. Rebar chairs are made in various heights and layouts to accommodate multi-layer steel cages, enabling intricate structural detailing. Drainage channels are available with aesthetic grates, which can blend seamlessly with surrounding materials like stone, tile, or paved surfaces.
For public or residential projects where appearance matters, plastics provide latitude for creative design without compromising the overall system's mechanical or chemical performance. This flexibility makes plastic construction elements suitable for courtyard terraces, pool surroundings, contemporary building facades, and many other visually demanding environments.
Potential Limitations and Mitigations
While plastics offer numerous advantages, they do have limitations in certain conditions. High-load environments like airports or heavy industrial settings may require more robust materials like metal or polymer concrete for drainage or rebar supports. Additionally, prolonged UV exposure can degrade some plastics, though stabilizers and coatings can mitigate this issue. Plastics also experience greater thermal expansion than metals or concrete, requiring proper design features like expansion joints or secure anchoring.
These challenges can be effectively managed by selecting the right plastic grade and following manufacturer guidelines. Careful planning ensures that plastics perform reliably in their intended applications.
Here are some key considerations for mitigating limitations:
Use reinforced materials for high-load scenarios.
Apply UV stabilizers or protective coatings for outdoor exposure.
Incorporate expansion joints to account for thermal movement.
Consult product specifications to match plastics to environmental and load conditions.
Need More Information?
From corrosion-resistant rebar chairs and reusable formwork to lightweight channel drains, high-quality plastics offer unmatched reliability while reducing labor and maintenance costs. These materials are designed to perform under diverse environmental conditions and simplify complex construction challenges.
While certain applications may require specific polymer grades or design adjustments, plastics' versatility and efficiency make them an invaluable choice for today’s builders and engineers. Whether you’re reinforcing concrete, managing surface water, or seeking cost-effective, durable solutions, plastics provide a smart path forward.
Learn More
Contact Piedmont Plastics to explore the best options for your next project and discover how our materials can streamline your construction process!
Request A Quote