Enhancing Safety and Installation
Plastics have played a transformative role in various industries, and the fluid-handling industry is no exception. With their versatility and many benefits, plastics offer solutions for a wide range of fluid-handling applications. Their industrial equipment utilization has revolutionized how fluids are stored, transported, and processed.
In the following sections, we will explore the different applications of plastics in fluid handling, their role in improving efficiency and reducing maintenance costs, and their mechanical properties. We will also discuss the various plastic materials used, including their chemical compatibility and corrosion resistance.

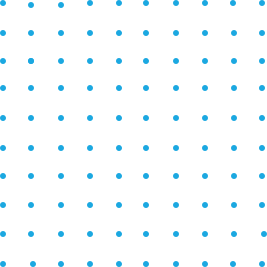
An Expert is just around the corner.
With over 100 years of combined product knowledge and industry experience, we are confident our plastics experts can help you find a solution for your application.
Environmental and Recyclability Advantages
In an era where sustainability is a top priority, plastics provide a greener alternative to traditional options like aluminum and stainless steel.
Plastic's most recognizable benefit is a reduced carbon footprint. Manufacturing plastic components requires less energy than metal or concrete, lowering greenhouse gas emissions.
They can also be recycled and reused, minimizing waste and resource consumption. By choosing plastics for fluid handling applications, industries can contribute to a more sustainable future and reduce their environmental impact.
Safety and Installation Benefits
Plastics offer many benefits regarding safety and ease of use in the fluid handling industry.
This raises the importance of corrosion resistance, which allows plastic materials to withstand exposure to water, chemicals, and other fluids without corroding or breaking down. This minimizes the risk of leaks or contamination.
Plastics are often manufactured with flame-retardant properties, providing an extra layer of safety. In the event of a fire, plastic components resist burning, reducing the spread of flames and potentially dangerous situations. Nylon, for example, offers a high heat resistance.
Plastics also offer hygienic properties, making them suitable for applications in industries such as food and pharmaceuticals. They can be easily cleaned and sanitized, preventing the buildup of harmful substances or contaminants that could compromise the safety and integrity of the fluid handling process.
Water Treatment Applications
Plastics play a crucial role in the fluid handling industry's portable and wastewater treatment processes. Their unique properties make them preferred for constructing pipes, valves, and storage tanks in water treatment applications.
We've already mentioned one advantage here: plastic's exceptional resistance to corrosion. Unlike traditional materials like stainless steel, plastics are not susceptible to rusting or degradation when exposed to water or various chemicals commonly found in treatment processes.
Besides corrosion resistance, plastics also boast excellent chemical compatibility. They can tolerate aggressive chemicals commonly used in water treatment, such as disinfectants and pH adjusters.
The following types of plastics are commonly used in water treatment:
High-density polyethylene (HDPE) is valued for its durability, chemical resistance, and flexibility, making it an excellent choice for constructing water pipelines and storage tanks.
Polyvinyl chloride (PVC) is known for its excellent corrosion resistance and affordability, making it popular for pipework and valves.
Polypropylene (PP) is often used for its good chemical resistance and tolerance to higher temperatures, making it suitable for handling aggressive chemicals.
Industrial Equipment Utilization
Plastics are vital in industrial equipment, particularly pumps, valves, and heat exchangers. They offer many advantages over traditional metal components, making them an ideal choice for these applications.
Plastics are known for maintaining their shape and structural integrity even under extreme temperatures and pressures. This stability ensures the proper functioning of pumps, valves, and heat exchangers, preventing leaks and optimizing performance.
Plastics also offer cost-saving benefits in terms of maintenance and replacement. Because of their corrosion resistance and dimensional stability, plastic components require less frequent maintenance and have longer service lives than metal counterparts. This translates to lower maintenance costs and reduced downtime for industrial equipment.
Alongside those mentioned above, you'll find these plastics used for industrial applications:
Polytetrafluoroethylene (PTFE), otherwise known as Teflon® (a registered trademark of DuPont), is widely used because of its high chemical resistance, stability across temperatures, and excellent electrical resistance.
Acrylonitrile Butadiene Styrene (ABS) is a rigid, compound thermoplastic with low moisture absorption, making it popular for automatic covers, shrouds, and housings.
Medical Fluid Handling
Plastics are crucial in medical fluid handling applications, particularly in medical equipment, diagnostics, blood processing, and dialysis. Using plastics in these processes ensures accurate fluid measurement, minimizes the risk of contamination, and maintains system reliability.
In diagnostics, plastics are essential for precisely measuring fluids, which is vital for accurate diagnosis. Plastic components, such as tubing, connectors, and valves, provide a sterile and reliable pathway for transporting and analyzing samples.
Plastics help maintain the blood sample's integrity and safety in blood processing. For example, blood bags are made from specialized medical-grade plastics store and collect blood. These biocompatible bags ensure the blood remains unaffected during storage and transportation. Plastic tubing is used to transfer blood between different processing steps safely.
In dialysis, using plastics is essential for providing a safe and effective treatment for patients with kidney failure. Dialysis machines use plastic components, such as tubing, dialyzers, and filters, to perform fluid purification. The dimensional stability of plastics is also crucial in dialysis, as it ensures consistent fluid flows and prevents any leakage or air ingress.
Here are some plastics you'll find across these medical applications:
Low Density Polyethylene (LDPE) is found in orthotics, medical tubing, and other medical equipment because of its great biocompatibility and corrosion resistance.
Acetal is a highly customizable application found in wire harness fixtures, sterilization trays, and some industrial applications.
Polycarbonate is a general-use plastic with excellent insulation capabilities and low moisture absorption, making it ideal for sterile environments.
Ultra-High Purity Fluid Systems
Ultra-high purity fluid systems require the utmost level of cleanliness and integrity to prevent contamination and maintain the quality of the fluid being stored or transported.
We've mentioned plastic's high resistance to chemical reactions earlier, which prevents contamination in ultra-high purity fluid systems. Plastics are highly inert, meaning they have minimal interaction with the stored or transported fluid.
This prevents any contamination or degradation of the fluid, ensuring its purity remains intact. For example, Saint-Gobain TYGON® 2475 High Purity Tubing can be found in cell culture and fermentation applications.
Future Prospects
As the world becomes more focused on sustainability and efficiency, the fluid handling industry also embraces emerging technologies and innovative solutions to meet these demands. Here are just two examples:
Smart systems, robotics, and the Internet of Things (IoT)
One of the key areas of advancement in fluid handling is the integration of smart systems, robotics, and the Internet of Things (IoT). These technologies can potentially enhance the efficiency and reliability of fluid handling applications.
Smart systems can monitor and control fluid flow in real-time, optimizing processes and minimizing waste. Robotics can automate previously labor-intensive tasks, increasing productivity and reducing the risk of human error.
The IoT enables seamless communication and data exchange between different components of a fluid handling system, allowing for enhanced coordination and predictive maintenance.
New materials
Another significant advancement in fluid handling is being driven by materials science. The development of new plastic resins and composite materials is revolutionizing the performance and reliability of fluid handling systems.
These materials offer superior chemical resistance, dimensional stability, and corrosion resistance compared to traditional materials like stainless steel. This enables the handling of aggressive chemicals, hot fluids, and abrasive substances with higher efficiency and durability.
Advances in materials science are also leading to the development of biodegradable plastics, which contribute to a more sustainable and environmentally friendly fluid-handling industry.
Need Help Buying?
The fluid handling industry is constantly evolving to meet the world's changing needs. It also depends upon the corrosion resistance, adaptability, and purity of plastics. Other materials, like steel, aren't cost-effective and fail to meet the needs of the modern fluid handling industry.
Learn More
Contact one of Piedmont Plastic's experts today to learn how plastics can help improve your fluid handling capabilities!