A Comprehensive Overview
In the stringently regulated food and healthcare sectors, the significance of material safety and adherence to regulatory standards cannot be overstated.
At Piedmont Plastics, we stand at the forefront of plastic material distribution, fully acknowledging the indispensable necessity of FDA-compliant plastics in these vital industries.
Our commitment revolves around offering businesses and individual consumers a range of superior-quality, FDA-compliant plastic sheets. These materials are needed to comply with rigorous health and safety regulations and play a pivotal role in safeguarding public health.
Therefore, our focus is on meticulously curating a selection of FDA-compliant plastics that meet the highest standards of safety and quality, thereby contributing positively to the overall well-being of the public and the business ecosystem that serves them.

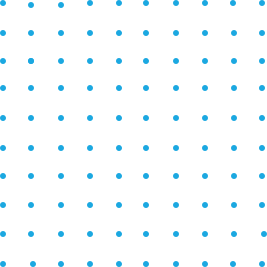
An Expert is just around the corner.
With over 100 years of combined product knowledge and industry experience, we are confident our plastics experts can help you find a solution for your application.
Defining FDA-Compliant Plastics
FDA-compliant plastics are those that meet the strict safety standards set by the U.S. Food and Drug Administration for materials used in direct contact with food or medical products. Understanding the difference between 'FDA-compliant' and 'FDA-approved' plastics is crucial. The former refers to materials adhering to FDA's safety guidelines, while the latter denotes materials that have received explicit FDA approval for specific applications.
This distinction is key in ensuring the correct material is used for each specific purpose.
Characteristics of FDA-Compliant Plastics
FDA-compliant plastics are meticulously selected for their specific attributes, ensuring their safety and effectiveness in food and medical applications. These plastics must adhere to strict FDA standards. Defining characteristics include:
Non-Toxicity: This is crucial for protecting consumer health, especially in applications where direct contact with food or sensitive medical items occurs.
Resistance to Bacterial Contamination: This attribute is fundamental for maintaining hygiene and safety, particularly in medical environments where sterility is a priority, and in food packaging to prevent contamination and safeguard public health.
Chemical Stability: These materials are chemically inert and do not react with foods or medicines. This stability is critical to preserving the integrity and efficacy of the products they come into contact with, ensuring they remain pure and effective for their intended use.
To remain FDA compliant, these plastics must consistently maintain quality and safety throughout their service life. This ongoing adherence to standards ensures the materials' long-term reliability and use, making them a dependable choice for various applications.
Popular FDA Compliant Plastics
Each type of plastic in our supply is selected for its unique properties, making them suitable for various specific applications.
Here are some of the most popular FDA-compliant plastics we provide:
Our FDA-Approved Materials:
-
Pros Of Using HDPE
High-density polyethylene (HDPE) is a highly-versatile petroleum-based thermoplastic polymer and one of the most commonly used materials in manufacturing today. Its molecular structure provides an impressive strength/density ratio and is greatly valued for applications where moisture resistance and cost-effectiveness are desired.
-
LDPE (Low Density Polyethylene)
Piedmont Plastics carries LDPE (low density polyethylene) sheet and rod for drape forming or vacuum forming containers, bottles, bags, and lab equipment.
-
Polyester
Piedmont Plastics supplies polyethylene terephthalate or polyester film (PET film), providing solutions for many applications and markets.
-
Best Uses For Polypropylene Plastic
Polypropylene is a thermoplastic polymer resin with a wide range of industrial and commercial applications.
Crucial Role in the Medical Field
In the healthcare sector, FDA-compliant plastics are crucial for safeguarding medications in pharmaceutical packaging and are integral to the manufacture of medical devices, thanks to their strength and sterilization compatibility.
These plastics meet rigorous biocompatibility standards, ensuring safety during direct patient contact, particularly in implants and prosthetics. Their versatility also fosters medical advancements, significantly improving patient care and safety, underscoring their indispensable role in modern healthcare.
Challenges in Manufacturing
Manufacturing and utilizing FDA-compliant plastics is a complex process with several significant challenges, each requiring careful consideration and strategic planning.
The following challenges underscore the complexity of working with FDA-compliant plastics and highlight the necessity for a balanced approach that prioritizes regulatory compliance and environmental sustainability:
Adherence to FDA Guidelines | Environmental Responsibility |
---|---|
Manufacturers are required to follow FDA regulations strictly. This involves: | In the context of increasing environmental awareness, manufacturers also need to: |
• Choosing materials that meet specific safety and compliance criteria | • Improve the recyclability of plastics to reduce environmental waste. |
• Designing products that precisely align with FDA regulatory standards. | • Incorporate sustainable practices throughout the production process. |
Contact Us For Expert Guidance
We invite you to explore our range of FDA-compliant plastic materials and consult with our experts for tailored solutions. Piedmont Plastics is your trusted partner in selecting the right FDA-compliant plastics for your needs.
Reach out to us today to learn more about our FDA-compliant plastic sheet options and how they can benefit your business, ensuring safety in critical food and medical applications.