Shaping the Future of Material Science
Engineered plastics are innovative materials specifically designed with superior mechanical, thermal, and chemical properties compared to standard plastics. The development of plastics began in the early 20th century with materials like Bakelite and celluloid, initially used for everyday items such as combs, buttons, and electrical insulators. Over time, advancements occurred, leading to the creation of high-performance plastics by incorporating fibers and composites.
These engineered plastics offer enhanced strength, stability, and resistance to extreme conditions, making them indispensable in modern industry. Their distinctive properties have driven their adoption across various sectors, including automotive, aerospace, medical, construction, and electronics.
Properties of Engineered Plastics
Engineered plastics surpass traditional materials like metal and wood in several key areas, particularly strength and durability. These high-performance plastics are designed to provide comparable, if not superior, tensile strength and longevity, ensuring they withstand wear and tear over extended periods.
Additionally, engineered plastics have excellent chemical resistance, making them ideal for environments exposed to harsh chemicals where metals might corrode and wood might degrade. Unlike traditional materials that may weaken or deform over time, engineered plastics maintain thermal stability under extreme temperatures and conditions.

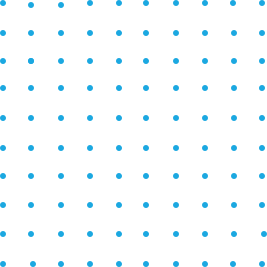
An Expert is just around the corner.
With over 100 years of combined product knowledge and industry experience, we are confident our plastics experts can help you find a solution for your application.
Technological Advancements
Engineered plastics are enriched through reinforcement techniques and innovative manufacturing processes, making them highly adaptable and robust. Using fibers and composites drastically improves the mechanical properties of plastics, such as strength, stiffness, and impact resistance.
Moreover, advanced fabrication methods such as injection molding and 3D printing allow for precise and efficient production of complex parts. Here are some key techniques and processes:
Fiber Reinforcement: Incorporation of glass, carbon, or aramid fibers to increase strength and durability.
Composite Materials: Combining different materials to achieve superior performance characteristics.
Injection Molding: A high-precision method for mass-producing intricate plastic components.
3D Printing: Enables rapid prototyping and custom manufacturing with complex geometries.
Thermoforming: Used to shape large plastic sheets into detailed parts through heat and pressure.
Environmental Impact
Engineered plastics are recyclable and reusable, reducing the need for brand-new materials and minimizing waste. This recyclability not only lessens environmental impact but also supports the development of sustainable manufacturing practices. Also, the production and use of engineered plastics generally consume less energy compared to traditional materials like steel.
In addition, engineered plastics’ lightweight nature reduces energy consumption in transportation and application, while advanced manufacturing processes streamline production, lowering energy requirements. These combined benefits result in more sustainable and energy-efficient industrial practices.
Potential Issues
While engineered plastics offer many advantages, they face challenges like heat resistance and structural support. Traditionally, many plastics would degrade or lose strength at high temperatures, and some lacked the structural integrity of metals. However, advancements in materials science are addressing limitations through the development of high-temperature-resistant polymers and reinforced composites that provide enhanced structural support.
Innovations such as long fiber reinforcements and the incorporation of nanoparticles are also significantly improving the thermal and mechanical properties of plastics. Emerging technologies such as bio-based polymers and smart materials promise to enhance the capabilities of engineered plastics further, making them even more versatile, sustainable, and high-performing for a wide range of applications.
Common Types of Engineering Plastics
Engineered plastics meet various industries' high-performance requirements, offering superior mechanical and thermal properties. These materials are designed for demanding applications where traditional plastics might not suffice.
Here are some universal types of engineered plastics:
Polyetheretherketone (PEEK): Known for its high-temperature resistance and mechanical strength, it is ideal for aerospace and medical applications.
Polycarbonate (PC): Offering excellent impact resistance and transparency, polycarbonate is widely used in automotive parts and electronics.
Acrylonitrile Butadiene Styrene (ABS): Combining strength and rigidity with easy processing, ABS is commonly used in automotive parts and consumer electronics.
Polytetrafluoroethylene (PTFE): Exhibiting outstanding chemical resistance and low friction, PTFE is used in chemical processing and non-stick applications.
Nylon (Polyamide): Known for its toughness and wear resistance, it is utilized in gears, bearings, and various mechanical components.
Environmental Effect
Engineered plastics contribute considerably to sustainability and energy efficiency in industries worldwide. Their recyclability allows these materials to be reused, reducing the need for additional resources and minimizing waste.
In addition, the production and use of engineered plastics typically require less energy compared to traditional materials like alloys and lumber. These combined benefits make engineered plastics fundamental for promoting green and energy-efficient industrial practices.
Challenges and Solutions
Engineered plastics have traditionally faced challenges such as heat resistance and structural support, but recent advancements are overcoming these limitations.
High-temperature-resistant polymers and reinforced composites now enhance thermal stability and mechanical strength, allowing plastics to perform in demanding environments. Innovations such as long fiber reinforcements and the integration of nanoparticles significantly improve these properties. Emerging technologies, including bio-based polymers and smart materials, also promise to further expand the capabilities of engineered plastics.
Applications in Key Industries
Engineered plastics have become integral in various industries due to their exceptional properties and resourcefulness.
Here are some places where these materials are making a big impact:
Automotive: Engineered plastics are used in vehicle components to reduce weight and enhance fuel efficiency, improving overall performance.
Aerospace: High-performance plastics help create stronger, lighter, and more efficient aircraft, improving fuel economy and reducing maintenance needs.
Medical: Biocompatible and sterilizable plastics are essential in manufacturing medical devices and equipment, ensuring safety and hygiene.
Construction: Engineered plastics enhance building materials, offering improved durability, sustainability, and resistance to environmental factors.
Electronics: Plastics are utilized in components requiring high heat resistance and electrical insulation, supporting the development of reliable and safe electronic devices.
Piedmont Plastics offers a wide range of high-performance plastics ideal for engineers, designers, machine shops, and fabricators. Our advanced materials, including PET, PBT, PEEK, Torlon®, Ultem®, and more, are renowned for their thermal stability, chemical resistance, and enhanced performance capabilities.
Ready to Buy?
Piedmont can meet your prototyping or specific application needs with a vast inventory that is ready for prompt shipment. Contact your local Piedmont branch today to speak with our experts and find your required high-performance plastic solutions.
Contact Us