How Autoclavable Plastics are Changing the Game
Autoclavable plastics are found across numerous industries. The steam sterilization process behind autoclaving allows for this flexibility. These plastics offer many benefits due to their ability to withstand high temperatures and sterilization processes. Understanding the versatility of autoclavable plastics is essential for realizing their potential applications and advantages.
This article will explore their pivotal role in medical device applications and the stringent safety standards they must meet. Additionally, we will examine the latest material innovations and their impact on sustainability and recyclability. By the end, you will have a comprehensive understanding of the advantages and advancements of autoclavable plastics compared to traditional materials. Join us as we uncover the fascinating journey of these remarkable plastics in the healthcare industry.

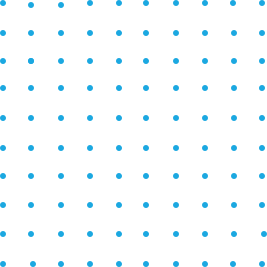
An Expert is just around the corner.
With over 100 years of combined product knowledge and industry experience, we are confident our plastics experts can help you find a solution for your application.
What are Autoclaves?
Autoclaves are machines used for sterilizing equipment and supplies by using intensely pressurized steam to eliminate bacteria, viruses, fungi, spores, and other microorganisms. They were invented in 1879 by microbiologist Charles Chamberland and are commonly used in medical and laboratory settings.
Autoclaves can withstand high temperatures and extreme pressure, making them suitable for treating highly regulated items. They are essential for ensuring safety in medical offices and are used to sanitize equipment in various areas of expertise, including scientific and medical purposes.
Medical Device Applications
The healthcare industry heavily relies on the versatility of medical-grade plastics, especially in the realm of surgical tools and medical containers. These plastics excel in creating various crucial items, from the precise grips and handles needed by surgeons to the robust trays used to sterilize instruments, such as:
Surgical Tools:
Handles and Grips: Designed for comfort and non-slip properties during procedures.
Sizing Trials: Used in joint replacements to gauge implant size.
Endoscopic Housings & Eyepieces: Provide durable protection for delicate equipment.
Medical Containers:
Sterilization Trays and Caddies: Engineered to endure the harsh environment of sterilization processes.
Diagnostic Equipment Parts: Components that ensure the functionality of X-ray and MRI machines.
Isolation Cubicles: Allow for the separation of patients in areas where they need more protection.
These products must comply with stringent safety and biocompatibility standards. They are integral to medical procedures, from the most basic to the most complex. Medical plastic products demonstrate exceptional performance in meeting these high demands, emphasizing their indispensable role in the medical device industry.
Sterilization Protocols
Safety is paramount in the medical device industry, and sterilization protocols play a critical role. When using an autoclave, sterilization protocols go through a four-step process.
FIRST: The autoclave is locked, so the plastics within are in a sealed chamber.
SECOND: A pump within the chamber removes air and replaces it with steam. Pressure is then applied to the steam, similar to a pressure cooker. This second stage is known as the purge phase.
THIRD: Pressurization continues as the steam is continuously applied to the chamber. The equipment inside is kept at consistent temperatures that allow for sterilization.
FOURTH: When the process is done, pressure is exhausted from the chamber, restoring the interior to the same pressure levels as the outside.
This four-step process enables chemical-free sterilization. This provides a method of sterilization for plastics that would normally react with some cleaning chemicals.
Alternative Sterilization
Here are a few alternatives to the autoclave process so you can consider alternative methods:
Ethylene Oxide (EtO) Sterilization:
A low-temperature method accommodating a broad spectrum of plastics, ideal for diverse medical devices and packaging.
Gamma Sterilization:
Employs Cobalt-60 gamma rays, effectively destroying pathogens. It is commonly used for single-use medical devices, covering over 40% of sterilizations.
Dry Heat Sterilization:
Operates at 160°C-170°C for at least two hours, necessitating plastics engineered for high heat tolerance, especially for medical packaging.
Plasma Sterilization:
It uses ionized gas, which is suitable for heat-sensitive applications and offers an alternative to traditional high-heat methods.
Medical plastics must meet rigorous safety and biocompatibility standards. Each sterilization technique requires plastic materials that can endure specific environmental conditions without degrading, ensuring aseptic medical tools are safely delivered to healthcare professionals.
Material Innovations for Autoclavable Plastics
The medical landscape is constantly evolving, and the demand for advanced autoclavable plastics with enhanced performance is increasing by about 5% per year. Researchers are pioneering novel plastic compositions tailored for the medical device industry, ensuring they can withstand rigorous sterilization cycles.
Recent innovations have led to energy-efficient autoclaves with smart technologies, such as IoT and cloud-connected data analytics, revolutionizing device packaging and assembly. These advancements streamline the sterilization process and strictly adhere to health standards, showcasing the synergy between technology and material science.
The evolution of plastic compositions stems from a deep understanding of polymer science. For example, the polymerization reactions and chemistry behind PE and PP are meticulously engineered to meet stringent medical requirements. This continuous development in autoclavable plastics heralds a new era of safe and reliable medical devices.
Common Autoclavable Materials
- PEEK (Polyetheretherketone)
- PTFE (Polytetrafluoroethylene)
- Polycarbonate
-
PMMA (Polymethyl Methacrylate)
-
COC (Cyclic Olefin Copolymer)
-
PFA (Perfluoroalkoxy Alkane)
-
FEP (Fluorinated Ethylene Propylene)
-
ETFE (Ethylene Tetrafluoroethylene)
-
Silicone
-
And more!
Environmental Impact of Autoclavable Materials
The role of autoclavable plastics extends beyond their vital function in various industries; these materials are key players in sustainability efforts. As these industries embrace reuse over single-use, autoclavable plastics are paramount in reducing waste.
In tandem with the reuse potential, manufacturers are now innovating recyclable autoclavable plastic compositions. These developments aim to foster a circular economy where materials are repurposed rather than discarded. The recyclability of these plastics is crucial as it minimizes their environmental footprint.
Recycling facilities rapidly adapt to accommodate these specialized plastics, paving the way for a more sustainable medical environment. Through proper disposal and repurposing, autoclavable plastics contribute to reducing carbon footprint.
Aligning with global initiatives for environmental responsibility, the advancement of sustainable autoclavable plastics is met with industry-wide support, reflecting the growing demand for eco-friendly alternatives in medical device materials.
Plastics vs. Traditional Materials
Medical grade plastics, particularly high-density polyethylene (HDPE) and polypropylene (PP), assert cost-effectiveness against traditional materials, shining in blow molding applications of lab items due to HDPE's robust chemical resistance and superior temperature endurance. These plastics, such as polymethylpentene (PMP or TPX), PP, trump glass, and metal, have unbeatable durability and resilience, making them exemplary for frequently sterilized healthcare tools.
Additionally, PMP and polycarbonate (PC) plastics surpass standard materials by offering chemical resistance, rigidity, and stability. However, LDPE and PP are notable for their resistance to a spectrum of acids and solvents. These attributes render them perfect for many laboratory essentials, balancing affordability with chemical resilience and structural integrity.
Material Characteristics | HDPE/PP | Traditional Materials |
---|---|---|
Chemical Resistance | Superior | Variable |
Impact Resistance | High | Lower |
Cost-Effectiveness | High | Moderate |
Temperature Resistance | High | Lower |
Sterilization Compatibility | Autoclavable | Limited |
Ready To Get Started?
Contact your local Piedmont Plastics sales rep today to learn how to use autoclavable plastics in your environment.
Contact Us