High-performance polymers (HPP) are a specialized class of engineering plastics designed to maintain structural integrity under extreme conditions, such as high heat, exposure to harsh chemicals, or significant mechanical stress. These materials are known for their exceptional flame-retardant properties and dimensional stability over time. While engineering plastics like polycarbonate or nylon provide moderate strength and temperature resistance, HPPs elevate these capabilities to new levels.
Several key factors determine whether a polymer qualifies as high-performance. These include a high glass transition temperature, an elevated melting point, and unique chemical structures offering exceptional flame or hydrolysis resistance. Although HPPs typically have a higher upfront cost, their extended service life and durability often offset the investment, making them a reassuringly cost-effective choice in demanding applications. This balance between superior performance and long-term value drives their adoption across various industries.
As one of North America’s largest plastic sheet, rod, tube, and film distributors, Piedmont Plastics has extensive experience supporting industries like aerospace, automotive, electronics, and medicine with high-performance materials. Whether it’s ensuring tight tolerances at elevated temperatures or resisting aggressive chemicals, advanced polymers like HPPs provide a reliable and efficient alternative to metals and lower-grade plastics in challenging environments, instilling confidence in their performance.

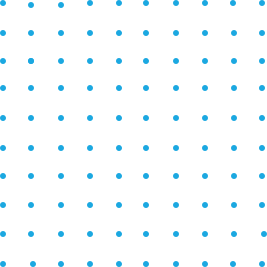
An Expert is just around the corner.
With over 100 years of combined product knowledge and industry experience, we are confident our plastics experts can help you find a solution for your application.
Why Manufacturers Love PEEK (Polyether Ether Ketone)
PEEK is widely regarded as the benchmark for high-performance polymers. As a semicrystalline thermoplastic with a melting point of approximately 343°C (649°F), it offers exceptional properties that make it indispensable for demanding applications. PEEK’s standout features include excellent chemical resistance, maintaining mechanical strength in high-temperature environments, and exceptional wear resistance, even under prolonged friction. These qualities have made it a go-to material in aerospace, medical, and oil and gas industries.
Chemically, PEEK is naturally flame-retardant and meets UL 94 V-0 standards without requiring flame-retardant additives. Its semicrystalline structure strikes a balance between rigidity and toughness, enabling it to endure significant mechanical stress.
Additionally, PEEK is highly resistant to hydrolysis, allowing it to withstand repeated exposure to steam or hot water without degrading its properties. Various grades of PEEK, including glass-filled, carbon-filled, and FDA-compliant versions, are available to tailor its performance for specific applications. These grades enhance attributes such as stiffness, reduced friction, or biocompatibility, giving engineers the flexibility to meet precise design requirements.
PEEK is commonly used in aerospace components, where reducing weight and ensuring high-temperature stability are critical. In the medical sector, it is preferred for instruments and devices that must endure regular sterilization cycles, including exposure to steam autoclaves. In the oil and gas industry, PEEK’s ability to withstand extreme downhole temperatures and corrosive fluids sets it apart as one of the few materials capable of thriving under such harsh conditions without premature failure.
Using PTFE (Polytetrafluoroethylene)
PTFE, best known by DuPont’s Teflon® brand, is a standout material for applications requiring an ultra-low coefficient of friction and exceptional chemical resistance. Its chemical structure, built on the extremely stable carbon-fluorine bond, makes its surface nearly impervious to adhesion and resistant to a wide range of corrosive chemicals. PTFE can perform reliably across an extensive temperature range, from cryogenic conditions to approximately 260°C (500°F), while keeping its physical integrity and excellent electrical insulating properties.
Industries that rely on PTFE include food and beverage production, where its non-reactive surface and ease of cleaning are essential, and chemical processing, where components like seals and gaskets must withstand aggressive substances without degrading. PTFE is also critical in high-frequency electronic components and semiconductor manufacturing, where its superior dielectric strength ensures consistent performance in sensitive equipment.
PTFE is available in different grades to suit specific needs. Virgin PTFE, made from pure resin, offers maximum chemical resistance and FDA compliance, making it ideal for applications involving food, pharmaceuticals, or high-purity requirements. Alternatively, mechanical or filled grades, which incorporate reprocessed resin or additives, offer cost-effective options, and can improve wear resistance or other performance characteristics depending on the filler material. These versatile options allow PTFE to meet the demands of diverse industries while balancing performance and cost.
Comparing Other High-Performance Polymers
While PEEK and PTFE are among the most recognized high-performance plastics, other advanced polymers offer unique benefits tailored to specific applications. Engineers may opt for alternative materials that balance performance with budget based on factors like heat resistance, mechanical strength, chemical compatibility, and cost. Here are some noteworthy options:
Polyphenylene Sulfide (PPS)
PPS offers strong heat and chemical resistance at a lower cost than PEEK, making it ideal for under-the-hood automotive parts and industrial applications.
Polyetherimide (PEI)
Known by brand names like Ultem™ or Duratron®, PEI provides inherent flame retardancy and exceptional strength, allowing it to maintain tight tolerances in high-temperature industrial and electronic settings.
Polysulfones (PSU, PES, PPSU)
These materials are durable, impact-resistant, and capable of withstanding repeated sterilization cycles, making them a reliable choice for medical devices and components.
Manufacturing and Processing Considerations
Processing high-performance polymers can be challenging due to their elevated melt temperatures and, in some cases, higher viscosities. For instance, PEEK may need injection molding equipment capable of operating at temperatures above 370°C (698°F). Molds must be made of materials that withstand repeated heating and cooling cycles without deformation. Pre-processing steps, such as thorough drying, are critical to ensure consistent results.
After molding, further finishing or CNC machining may be necessary, especially for components with tight tolerances. This process requires tool materials to handle the hardness or potential abrasiveness of certain filled grades (like carbon- or glass-filled PEEK). In many cases, manufacturers will anneal parts after forming or machining to relieve residual stresses, thereby enhancing the dimensional stability and longevity of the final product.
Where Advanced Plastics Are Used
High-performance polymers are essential for industries that demand both reliability and efficiency. Their unique properties make them indispensable across a range of sectors:
Aerospace: Lightweight and heat-resistant, these materials are ideal for engine components and structural parts that must endure vibration, thermal fluctuations, and demanding operational conditions.
Automotive: Advanced polymers like PEEK and PPS are commonly used in sensors, gears, and fuel system parts, where they provide excellent resistance to chemicals and high temperatures.
Electronics and Semiconductors: Materials like PTFE and PEI offer stable electrical properties, protecting delicate circuitry while minimizing outgassing. This makes them perfect for cleanroom environments and precision manufacturing.
Medical Devices: Sterilization-friendly polymers such as PEEK and polysulfones withstand repeated autoclaving without warping or degradation, ensuring durability in surgical instruments and other healthcare applications.
Industrial Equipment: In pumps, mixers, and conveyor systems, advanced plastics are used for gaskets, seals, and bearings due to their ability to resist abrasive wear and corrosive fluids, extending the lifespan of critical components.
Sustainability and Lifecycle Advantages
The durability of engineering plastics allows components to last longer, reducing the frequency of replacements and conserving energy and raw materials. While high-performance polymers are not always as easily recyclable as commodity plastics, many can be reprocessed or downcycled depending on their grade and level of contamination.
Even when recycling is not a viable option, the extended life of these materials significantly reduces waste compared to lower-grade alternatives that fail more quickly.
Partnering for High-Performance Solutions
For over 50 years, Piedmont Plastics has been a trusted partner for businesses needing advanced plastic solutions. With multiple locations across North America, we offer an extensive inventory of high-performance polymers, including PEEK, PTFE, PPS, PEI, and polysulfones. Our experienced team is here to help you choose the best materials for your unique needs, manage logistics, and provide cut-to-size services or even custom fabrication.
Quality is our priority. We partner with leading suppliers like Mitsubishi Chemical Advanced Materials and Victrex to deliver certified, traceable materials that meet strict standards for FDA compliance, medical use, flame resistance, and more. With a streamlined supply chain and quick delivery from our nationwide network, we make it easy for you to integrate high-performance plastics into your designs.
Talk to Our Experts
Ready to get started? Contact your local branch to discuss your project and request a quote.
Send Us A Message